huide
wire spring forming machine factory
Place of Origin | China |
Condition | New |
Machine Type | wire spring forming machine factory |
Core Components | PLC, Engine, Bearing, Gearbox, Motor, Pressure vessel, Gear, Pump |
Weight (KG) | 2072 |
Key Selling Points | Competitive Price |
Warranty | 1 years |
Applicable Industries | interior decoration |
Raw Material | Carbon steel, SS |
Material / Metal Processed | ALLOY |
Product name | wire spring forming machine factory |
Keyword | steel wire forming machine |
Wire diameter | 12.74mm-17.08mm |
Wire type | Square, Round wire bending |
Marketing Type | Ordinary Product |
Payment terms | 30%T/T in advanced payment,the left payment should be paid after we finish our production.( we will take machine and packing photos for your checking ) We have our own forwarder. We can check the delivery information timely. |
Packing | In standard export wooden case for wire bending Machine Delivery time:within 15 days after receiving your |
Wire forming machine is suitable for various metals | (such as steel, iron, stainless steel, aluminum wire, etc.) |
Features | Twisting head is designed in copper tube transport, more stable and stronger than bearing transfer Technical parameters(3d cnc wire bending machine suppliers) |
wire spring forming machine factoryApplication Field
Movable bearings in the inner and outer molds enable trace,
Graphic input 2d wire forming machine diameter range 2- 10mm
wire bending machine manufacturers-OEM/ODM service is available. Low MOQ, we can accept low MOQ as 9 sets, or even less quantity for every single item in big production order. We have full experience in exporting and project management, to secure your order 100%.
wire spring forming machine factory services FAQs Guide Are you looking for a quick review guide about wire spring forming machine factoryservices? An ultimate FAQ buying guide is available to help you.This guide contains all the information about all the important facts, figures, and various processes regarding wire spring forming machine factory services. Let’s continue!
2.What is the expected lifespan of a wire spring forming machine factory?
3.How does a CNC wire spring forming machine factory differ from a manual wire spring forming machine factory?
4.About wire spring forming machine factory warranty
5.Is it possible to automate the bending process with a wire spring forming machine factory?
6.What are the most common applications for a wire spring forming machine factory?
7.About wire spring forming machine factory origin
8.How can the accuracy of a wire spring forming machine factory be improved?
9.About wire spring forming machine factory MOQ
10.About wire spring forming machine factory customization services
11.What are the different bending methods used in a wire spring forming machine factory?
12.About wire spring forming machine factory production capacity
13.About the development history of wire spring forming machine factory factory
14.What are the maintenance requirements for a wire spring forming machine factory?
1.What are the different types of wire spring forming machine factorys?
Our company has many years of wire spring forming machine factory experience and expertise. 1. Hydraulic Press Brake: This type of bending machine uses a hydraulic cylinder to apply pressure to a workpiece in order to bend it. 2. Mechanical Press Brake: This type of bending machine uses a mechanical ram to apply pressure to a workpiece in order to bend it. 3. Roll Bending Machine: This type of bending machine uses a set of three or more rolls to bend a workpiece. 4. Sheet Metal Bending Machine: This type of bending machine is used to bend sheet metal into various shapes. 5. Tube Bending Machine: This type of bending machine is used to bend tubes into various shapes. 6. CNC Bending Machine: This type of bending machine is computer-controlled and can be programmed to bend a workpiece into a specific shape.
2.What is the expected lifespan of a wire spring forming machine factory?
We adhere to the principle of quality first and have a complete production quality management system and quality inspection process. There are two main factors that affect the service life of line forming equipment: one is whether the operator's operation is scientific and standardized, and the other is reasonable daily maintenance. Here we mainly talk about the regular maintenance of line forming equipment. Its main function is to avoid accelerating the aging of the machine. The so-called daily maintenance of wire forming equipment refers to things that must be done almost every day, but the content is relatively simple and easy, mainly including the cleaning, lubrication, inspection and tightening of the machine, etc.The second is the regular maintenance of line forming equipment: regular maintenance is slightly different from daily maintenance. The time interval of regular maintenance is relatively long and does not need to be carried out every day. It is usually after the working hours specified for machine maintenance are reached or exceeded, but the content of maintenance There are relatively many and complex ones. Its maintenance content mainly includes the following contents: 1. Check and adjust the working conditions of transmission, clutch, engine, transmission mechanism, braking mechanism, steering and working devices, servo system and electrical system; 2. Detect and eliminate hidden faults, and balance the wear and tear of each component; 3. All relevant fasteners should be lubricated and cleaned regularly; 4. If it is not used for a long time, it should be deactivated and maintained, and cleaning and anti-corrosion work should be done.
3.How does a CNC wire spring forming machine factory differ from a manual wire spring forming machine factory?
Our products & services cover a wide range of areas and meet the needs of different fields. A CNC bending machine is a computer-controlled machine that uses a programmable logic controller (PLC) to control the bending process. It is capable of producing complex bends with high accuracy and repeatability. It is also able to produce multiple bends in a single operation. A manual bending machine is operated manually and requires the operator to manually adjust the bending angle and pressure. It is not as accurate or repeatable as a CNC bending machine and is limited to producing simple bends. It can be completed from modulation, wire feeding, bending, cutting, all on one machine at one time. However, with a manual bending machine, you need to straighten and cut the wire on the straightening and cutting machine first, and then manually put it on the bending machine. bending. Moreover, the working efficiency of intelligent bending machines is much higher than that of manual bending machines, saving labor costs.
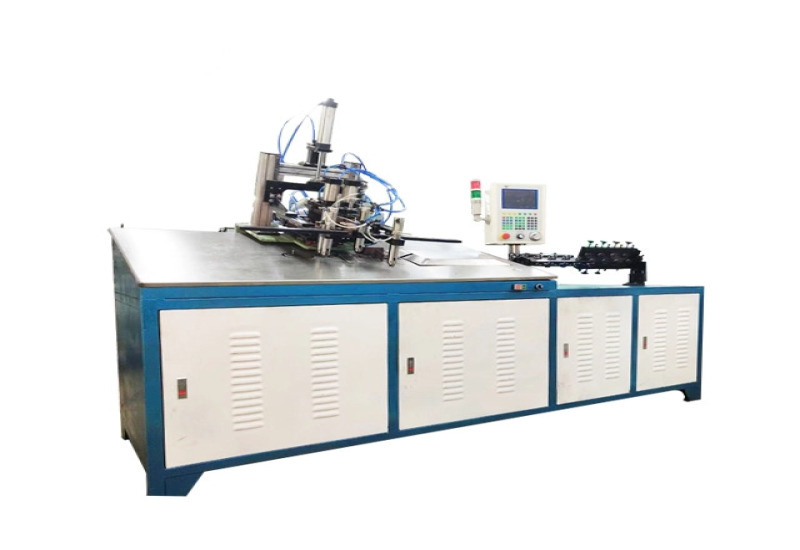
4.About wire spring forming machine factory warranty
Starting from the receipt of the bill of lading, if it is not caused by human factors, the whole machine is guaranteed for one year. If the machine parts are damaged due to the reason, we will provide the machine parts at the cost price, but the customer needs to bear the freight.
5.Is it possible to automate the bending process with a wire spring forming machine factory?
Our wire spring forming machine factory products undergo strict quality control to ensure customer satisfaction. A wire bending machine is a device that can bend metal wires at specified angles and shapes. It is widely used in electronics, communications, automobiles, home appliances and other industries to produce various wire components and electrical wiring harnesses. The emergence of wire bending machines has greatly improved production efficiency, reduced manual labor intensity, and ensured the stability of product quality.
6.What are the most common applications for a wire spring forming machine factory?
We focus on innovation and continuous improvement to maintain a competitive advantage. 1.Auto Industry area 2.Metal wire industry 3.Display table and cargo shelf 4.Furniture and Kitchen 5.Hardware industry 6.Mattress, Sofa spring area 7.Architecture area 8.Hardware Artcraft
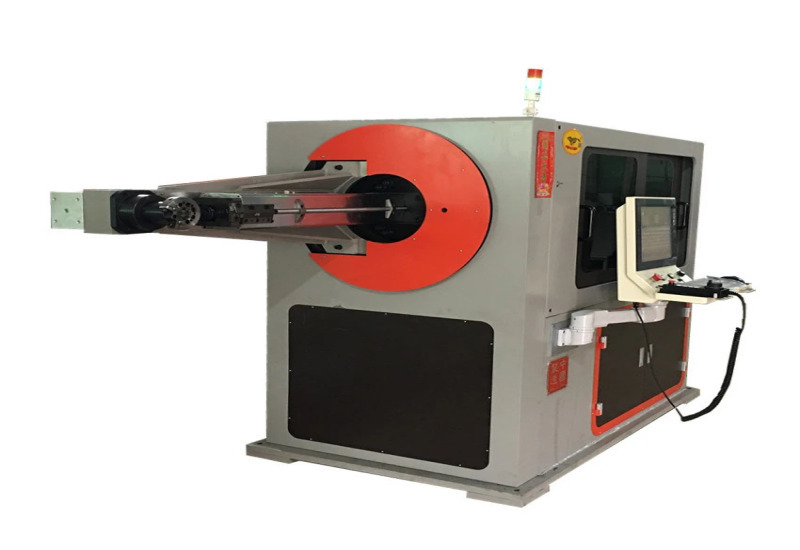
7.About wire spring forming machine factory origin
The servo motors and electrical components are imported brands, and the machine frame is cut and manufactured by our factory.
8.How can the accuracy of a wire spring forming machine factory be improved?
As one of the wire spring forming machine factory market leaders, we are known for innovation and reliability. 1. Regularly inspect and maintain the machine to ensure that all components are in good working order. 2. Use high-quality materials for the machine components. 3. Use a high-precision measuring device to ensure accuracy. 4. Use a high-precision cutting tool to ensure accuracy. 5. Use a high-precision bending tool to ensure accuracy. 6. Use a high-precision clamping system to ensure accuracy. 7. Use a high-precision control system to ensure accuracy. 8. Use a high-precision feedback system to ensure accuracy. 9. Use a high-precision lubrication system to ensure accuracy. 10. Use a high-precision cooling system to ensure accuracy.
9.About wire spring forming machine factory MOQ
1set can be acceptable for trail order.
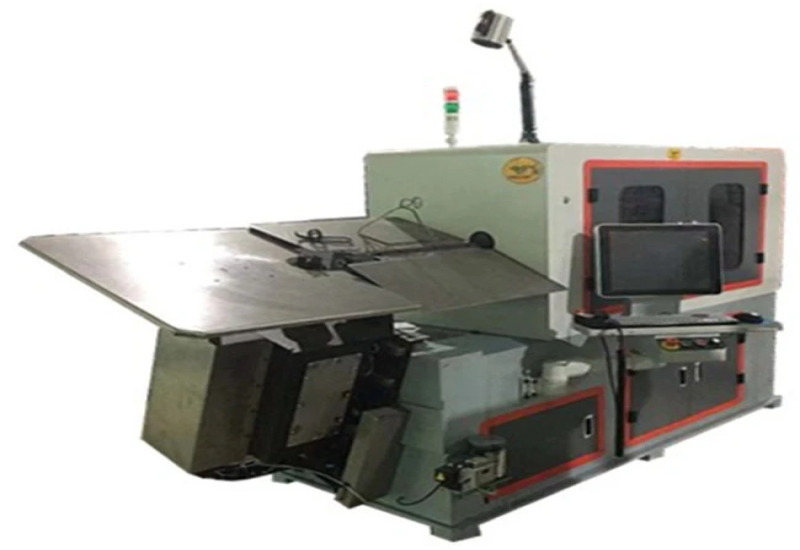
10.About wire spring forming machine factory customization services
We can design customized machines according to customers' special drawing requirements, and also accept OEM services.
11.What are the different bending methods used in a wire spring forming machine factory?
We adhere to the principle of quality first and have a complete production quality management system and quality inspection process. (1) Free bending The free bending method is the most commonly used method. Free bending uses the two edges at the opening of the die and the edge at the top of the punch to perform bending. The bending angle is determined by the depth of the punch entering the die. The bending force required for free bending is smaller, the stress on the mold is gentler, and the service life of the mold can be extended. The disadvantage is that the thickness of the sheet, the inconsistency of the mechanical properties, and the rolling direction of the steel plate will cause changes in the bending angle. (2) Correction of bending Corrective bending is when the punch presses the rounded corners and straight edges of the workpiece. During the downward movement of the punch, the angle of the blank will be smaller than the angle of the concave mold, resulting in negative rebound; at the end of the stroke, the punch and concave mold will correct the blank so that its rounded corners, straight edges, and bending radii are all close to the punch. . It can be seen that corrective bending can effectively overcome the rebound effect, thereby achieving high bending accuracy. (3) Three-point bending To process this part with a CNC press, you only need to program it and clamp and position it once to complete the entire processing. The programming time is two to three hours at most, the processing time is only a few minutes, and the processing accuracy is high. The hydraulic pad pressure is evenly distributed over the entire bending length, so that the bending force of the punch is evenly distributed over the entire bending length. Each punch is elastically supported, so it can automatically adapt to the bending straightness of the die and ensure constant pressure distribution, thus improving the accuracy of the bending angle and the straightness of the bending edge. The bending angle error of the three-point bending method is ±15 degrees, which is equivalent to the accuracy of corrected bending. The bending thickness can reach 20mm. When the plate thickness exceeds 3mm, the three-point bending method is the only way to obtain the bend. This is because, in addition, if you want to obtain the same bending accuracy, you can only use correction bending, but the bending force will exceed the pressure limit that the mold can withstand.
12.About wire spring forming machine factory production capacity
50sets/month
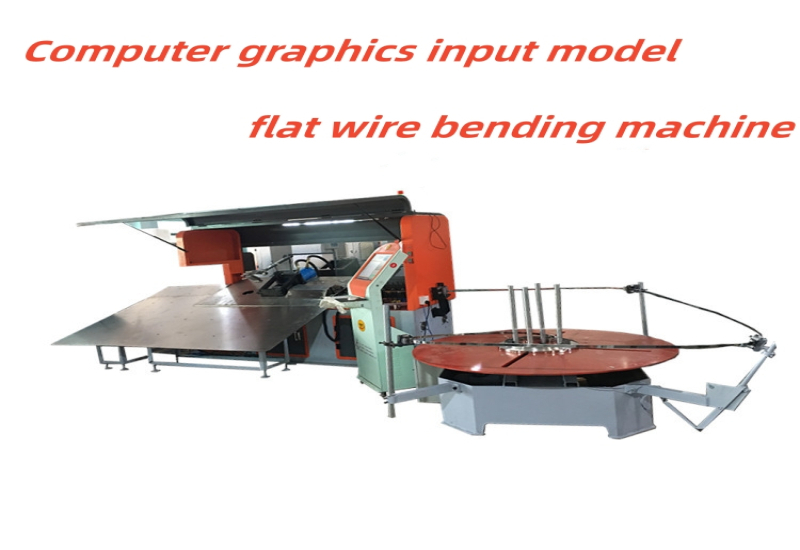
13.About the development history of wire spring forming machine factory factory
Huide Machinery Manufacturing Co., Ltd. was established in 2008. It is an innovative and creative enterprise specializing in metal wire forming, integrating R&D, design, production, sales and service. In the past 15 years of development, the company has always adhered to customer-oriented Demand-oriented, with product quality as the foundation, technological innovation as the basis for development, and customer service as the basis for market expansion, we work tirelessly and continuously to advance, and are always committed to maximizing the interests of business owners, operators, and employees. Today, Huide's products are sold all over the world and are exported to more than 120 countries. It accounts for more than 60% of the domestic peer market and 75% of the world's share. Its overall strength and various economic indicators of its products have ranked among the best in the country for many years. It ranks among the best in the industry and is recognized as a leader in the same industry in China.
14.What are the maintenance requirements for a wire spring forming machine factory?
We have established long-term and stable partnerships with our suppliers, so we have great advantages in price and cost and quality assurance. The maintenance of wire forming machines is very important. The following are some common maintenance methods: 1. Cleaning: Clean the equipment regularly, including removing dust, oil and other debris. You can use a soft cloth or brush to wipe the surface of the device and clean it with an appropriate detergent. 2. Lubrication: Lubricate the moving parts of the equipment regularly to ensure normal operation. Use an appropriate lubricant and lubricate according to the equipment manufacturer's recommendations. 3. Check fasteners: Regularly check bolts, nuts and other fasteners on your equipment to make sure they are tight. If there is any looseness, tighten it in time. 4. Regular inspection: Regularly inspect various components of the equipment, including electrical components, transmission systems, control systems, etc., to ensure their normal operation. If abnormalities or failures are found, they should be repaired or replaced in time. 5. Prevent dust and dirt from entering the inside of the equipment: During use of the equipment, attention should be paid to preventing dust and dirt from entering the inside of the equipment, so as not to affect the normal operation of the equipment. Dust covers or other appropriate measures may be used to protect equipment.