huide
thread rolling machines parts hs code
Our leading technology, advanced equipment, scientific management and perfect after-sales service are your confident assurance. In the marketing philosophy of Credit First
Product name | thread rolling machines parts hs code |
Keyword | quality thread rolling machine,thread rolling machine bhosari,thread rolling machine working,china thread rolling machine,mtr thread rolling machine,rib peeling blade for rebar thread rolling machine,bolt thread rolling machine supplier,thread rolling machine hs code no |
Place of Origin | China |
Production Capacity | 240~400/Per Min |
Power | 2.2~6kw |
Thread Dia(mm) | 2.0~4.0 |
Thread Length(mm) | 9~50 |
Feature | pipe nipple threading machine in its rolling pressure range of cold, the workpiece for thread, ruled, twill and other treatment; straight, helical and oblique spline gear rolling; straightening, reducing diameter, rolling and various forming rolling. |
Dimensions | 1740mm*1845mm*2070mm, (Contact us for specific information to confirm) |
Applicable Industries | Building Material Shops, etc. |
Color | orange or customized |
Weight | 2106kg |
Product Description | The machine has a safe and reliable electro-hydraulic execution and control system. Each work cycle can be selected in manual, semi-automatic and automatic ways. |
terms of packing | enerally, we pack our goods in plywood cases. |
terms of paymen | T/T 30% as deposit, and 70% balance against BL copy |
Life span | 12 years (Contact us for specific information to confirm) |
After-sale service | 12 months warrantly, man-made destory will be exception. |
thread rolling machines parts hs code Advantage | We keep good quality and competitive price to ensure our customers benefit |
Packing | 2043x2730x2040mm(Contact us for specific information to confirm) |
OEM/ODM | Customization Service Provided |
Sales country | All over the world for example:Nicaragua,Saint Lucia,Solomon Islands,Belgium,Slovakia,Tuvalu,Spain,Chad |
MOQ | 7pcs(Contact us for specific information to confirm) |
Delivery time | 15-20 days for OEM, 5-7days for ready goods. |
thread rolling machines parts hs code
huide-machinery.as one of the most professional thread rolling machines parts hs code manufacturer has the advantages at:
We are the leader thread rolling machine supplier in China, also we have customers worldwide, such as America, Argentina, Brazil, Belarus, Bangladesh, Nicaragua,Saint Lucia,Solomon Islands,Belgium,Slovakia,Tuvalu,Spain,Chad, and Italy.We are factory specializing in the manufacture and export of thread rolling machine for more than 20 years, all of the production we sale are at a very best price and high quality.
We take care of our product quality, any defect of the goods, we will take responsibility. You are risk-free.And we believe that the good quality products will can give us survival, so, we always offer the top quality products to our customers, to keep them have the competitiveness in there market.
thread rolling machines parts hs code services FAQs Guide
Are you looking for a quick review guide about thread rolling machines parts hs codeservices?
An ultimate FAQ buying guide is available to help you.This guide contains all the information about all the important facts, figures, and various processes regarding thread rolling machines parts hs code services.
Let’s continue!
2.What are the Limitations of a thread rolling machines parts hs code?
3.What does your factory produce ?
4.How Does the Thread Rolling Process Work?
5.How does the thread rolling process compare to other methods such as chasing or grinding?
6.What Types of Materials can be Used with a thread rolling machines parts hs code?
7.Can a thread rolling machines parts hs code create threads on hardened materials?
8.What is the lifespan of a thread rolling machines parts hs code?
9.How long does it take to set up and operate a thread rolling machines parts hs code?
10.Can a thread rolling machines parts hs code create threads on curved or irregular surfaces?
11.What is the maximum thread size that can be rolled with this machine?
12.How does a thread rolling machines parts hs code contribute to the accuracy and precision of threaded parts?
13.Can a thread rolling machines parts hs code Create Threads with Different Tolerances?
14.What are the Main Components of a thread rolling machines parts hs code?
1.What is the Typical Production Rate of a thread rolling machines parts hs code?
The typical production rate of a thread rolling machine can vary depending on the type and size of the machine, as well as the material being rolled. However, on average, a thread rolling machine can produce between 60 to 120 parts per minute. Some high-speed machines can even produce up to 300 parts per minute.
2.What are the Limitations of a thread rolling machines parts hs code?
Our thread rolling machines parts hs code products undergo strict quality control to ensure customer satisfaction.
1. Limited to cylindrical parts: Thread rolling machines are only suitable for producing threads on cylindrical parts. They cannot be used for producing threads on non-cylindrical or irregularly shaped parts.
2. Limited thread size range: Thread rolling machines have a limited range of thread sizes that they can produce. This is determined by the size of the thread rolling dies used in the machine.
3. Limited thread types: Thread rolling machines are designed to produce only straight threads. They cannot produce tapered or helical threads.
4. High initial cost: Thread rolling machines are expensive to purchase and set up, making them less accessible for small businesses or hobbyists.
5. Limited material compatibility: Thread rolling machines are not suitable for all types of materials. They work best with softer materials such as aluminum, brass, and low carbon steel.
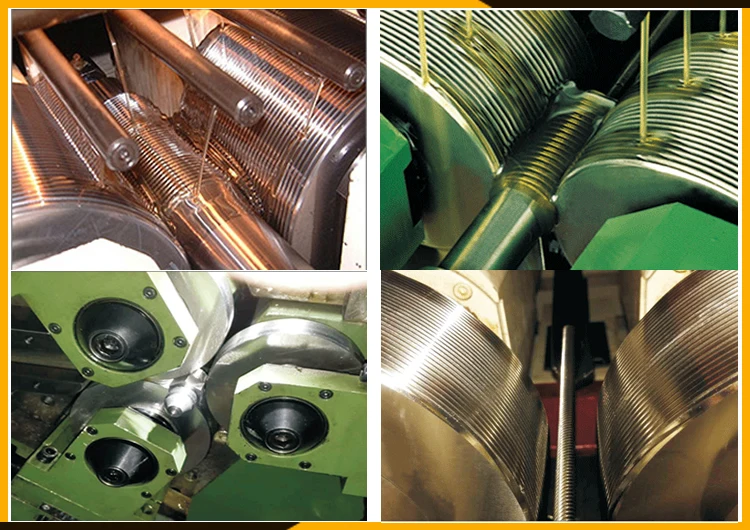
3.What does your factory produce ?
We produce and export all kinds of Reinforced Bar Thread Rolling Machine with butt welding. We also can design and develop automatic wire ring making machines with butt welding according to your requirements.
4.How Does the Thread Rolling Process Work?
We attach importance to the innovation ability and team spirit of employees, have advanced R & D facilities and laboratories, and have a good quality management system.
The thread rolling process is a cold forming process used to create external threads on a workpiece. It involves pressing a hardened steel die onto the surface of the workpiece, causing the material to flow and form the desired thread shape.
The process begins with a blank workpiece, typically a cylindrical rod or bar, which is fed into the thread rolling machine. The machine consists of two dies, an upper and a lower die, which are mounted on parallel spindles and rotate in opposite directions.
The upper die is stationary, while the lower die is adjustable and can be moved up and down to accommodate different thread sizes. The dies are also equipped with thread profiles that correspond to the desired thread shape.
As the workpiece is fed between the two dies, it is gripped and held in place by a set of rollers. The rollers apply pressure to the workpiece, forcing it to deform and flow into the thread profile of the dies.
The dies then rotate, causing the material to be displaced and formed into the desired thread shape. The pressure and rotation of the dies continue until the thread is fully formed.
Once the thread is formed, the dies retract, and the workpiece is released. The thread is then checked for accuracy using gauges and other measuring tools.
The thread rolling process is highly efficient and can produce threads at a much faster rate than traditional cutting methods. It also results in a stronger and more precise thread, making it a preferred method for creating high-quality threads in mass production.
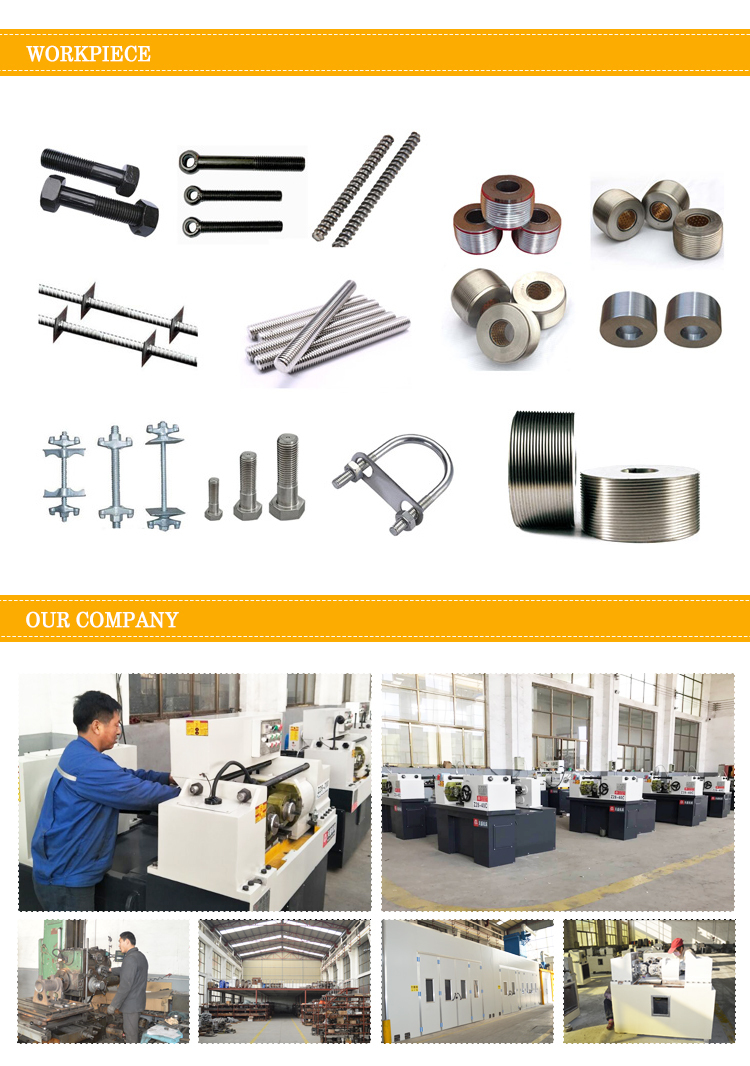
5.How does the thread rolling process compare to other methods such as chasing or grinding?
We should have a stable supply chain and logistics capabilities, and provide customers with high -quality, low -priced thread rolling machines parts hs code products.
Thread rolling is a cold forming process that uses hardened steel dies to deform the surface of a cylindrical blank, creating the desired thread profile. This process is typically used for high volume production of precision threads and offers several advantages over other methods such as chasing or grinding.
1. Faster Production Speed: Thread rolling is a high-speed process that can produce threads at a rate of up to 1000 parts per minute. This is significantly faster than chasing or grinding, which are typically slower processes.
2. Improved Thread Strength: The cold forming process of thread rolling results in a work-hardened surface that is stronger and more durable than threads produced by chasing or grinding. This makes thread rolling ideal for applications that require high strength and reliability.
3. Better Surface Finish: Thread rolling produces a smooth and precise thread surface, which is important for applications that require a tight fit or smooth movement. Chasing and grinding can result in rougher surfaces that may require additional finishing processes.
4. Cost-Effective: Thread rolling is a cost-effective process, especially for high volume production. The use of hardened steel dies also makes it a more durable and long-lasting method compared to chasing or grinding, which may require frequent replacement of tools.
5. Versatility: Thread rolling can be used to produce a wide range of thread sizes and profiles, making it a versatile process for various applications. It can also be used on a variety of materials, including steel, aluminum, and plastic.
In comparison, chasing and grinding are more suitable for smaller production runs or for repairing damaged threads. They also require more skilled labor and may result in higher costs for tooling and setup. However, they may be more suitable for producing specialized or non-standard thread profiles.
Overall, thread rolling offers a faster, more cost-effective, and versatile method for producing high-quality threads, making it a preferred choice for many industrial applications.
6.What Types of Materials can be Used with a thread rolling machines parts hs code?
We continue to invest in research and development and continue to launch innovative products.
1. Metal: Thread rolling machines are primarily used for rolling threads on metal materials such as steel, aluminum, brass, and copper. These materials are commonly used in industries such as automotive, aerospace, and construction.
2. Plastic: Some thread rolling machines are also capable of rolling threads on plastic materials such as nylon, PVC, and acrylic. These materials are commonly used in industries such as electronics, medical, and consumer goods.
3. Wood: Thread rolling machines can also be used to create threads on wooden materials such as hardwood and softwood. These threads are commonly used in furniture making and woodworking industries.
4. Composite materials: Thread rolling machines can also be used to roll threads on composite materials such as carbon fiber, fiberglass, and Kevlar. These materials are commonly used in industries such as aerospace, marine, and sports equipment.
5. Rubber: Some thread rolling machines are also capable of rolling threads on rubber materials such as silicone, neoprene, and EPDM. These materials are commonly used in industries such as automotive, construction, and medical.
6. Ceramic: Thread rolling machines can also be used to create threads on ceramic materials such as porcelain, clay, and glass. These materials are commonly used in industries such as pottery, construction, and electronics.
7. Other materials: Depending on the type and capabilities of the thread rolling machine, it may also be able to roll threads on other materials such as leather, paper, and fabric. These materials are commonly used in industries such as fashion, packaging, and upholstery.
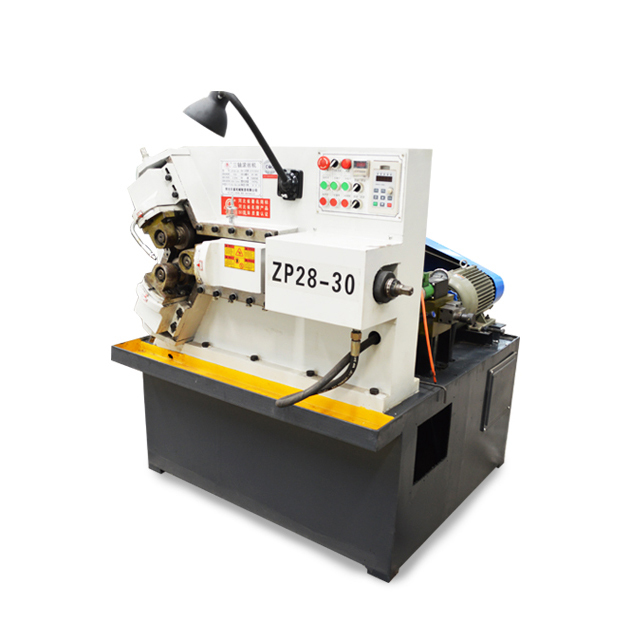
7.Can a thread rolling machines parts hs code create threads on hardened materials?
Our company has many years of thread rolling machines parts hs code experience and expertise.
Yes, a thread rolling machine can create threads on hardened materials.
The process of thread rolling involves pressing a hardened steel die onto the surface of the material, which displaces the material and forms the threads. This process is suitable for creating threads on a wide range of materials, including hardened materials such as stainless steel, titanium, and hardened steel. However, the hardness of the material may affect the speed and efficiency of the thread rolling process. It is important to use the appropriate die and machine settings for the specific material being threaded to ensure the best results.
8.What is the lifespan of a thread rolling machines parts hs code?
We should perform well in market competition, and the prices of thread rolling machines parts hs code products have a great competitive advantage.
The lifespan of a thread rolling machine can vary depending on factors such as usage, maintenance, and quality of the machine. On average, a well-maintained thread rolling machine can last for 10-15 years. However, with proper care and regular maintenance, some machines can last for 20 years or more.

9.How long does it take to set up and operate a thread rolling machines parts hs code?
We should enjoy a good reputation in the industry, and we can increase the added value of the products of cooperative customers through technological innovation.
The time it takes to set up and operate a thread rolling machine can vary depending on the specific machine and the experience of the operator. Generally, it can take anywhere from 15 minutes to an hour to set up the machine, including adjusting the dies and making any necessary adjustments. Once the machine is set up, the actual operation can take anywhere from a few seconds to a few minutes, depending on the length and complexity of the thread being rolled. With practice and experience, an operator can become more efficient and reduce the setup and operation time.
10.Can a thread rolling machines parts hs code create threads on curved or irregular surfaces?
As one of the thread rolling machines parts hs code market leaders, we are known for innovation and reliability.
No, a thread rolling machine is designed to create threads on flat or cylindrical surfaces only. It cannot create threads on curved or irregular surfaces.
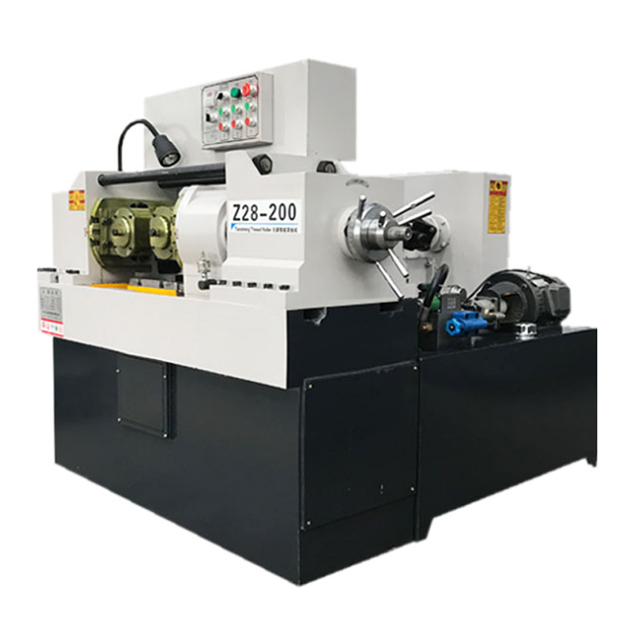
11.What is the maximum thread size that can be rolled with this machine?
As one of the top thread rolling machines parts hs code manufacturers in China, we take this very seriously.
The maximum thread size that can be rolled with this machine depends on the specific model and specifications of the machine. It is best to consult the manufacturer or the machine's manual for the exact maximum thread size.
12.How does a thread rolling machines parts hs code contribute to the accuracy and precision of threaded parts?
We are committed to providing personalized solutions and established long -term strategic cooperative relationships with customers.
A thread rolling machine contributes to the accuracy and precision of threaded parts in several ways:
1. Consistent Thread Profile: Thread rolling machines use a set of dies to form the threads on a workpiece. These dies are precisely machined to create a specific thread profile, ensuring that each thread is identical in shape and size. This results in a more accurate and precise thread compared to other methods such as cutting or grinding.
2. Uniform Thread Pitch: The dies on a thread rolling machine are designed to maintain a constant thread pitch throughout the entire length of the thread. This ensures that the threads are evenly spaced and have a consistent depth, leading to better accuracy and precision.
3. Reduced Material Deformation: Thread rolling machines use a cold forming process, where the material is not subjected to high temperatures. This reduces the risk of material deformation, which can affect the accuracy and precision of the threads.
4. Tight Tolerances: Thread rolling machines are capable of producing threads with tight tolerances, often within a few thousandths of an inch. This level of precision is difficult to achieve with other methods, making thread rolling a preferred choice for high-precision applications.
5. Repeatable Results: The use of dies and a controlled process in thread rolling ensures that the same results are achieved every time. This makes it easier to produce large quantities of threaded parts with consistent accuracy and precision.
Overall, a thread rolling machine offers a more controlled and precise method of creating threads, resulting in higher accuracy and precision of threaded parts. This makes it a preferred choice for industries such as automotive, aerospace, and medical, where precision is critical.
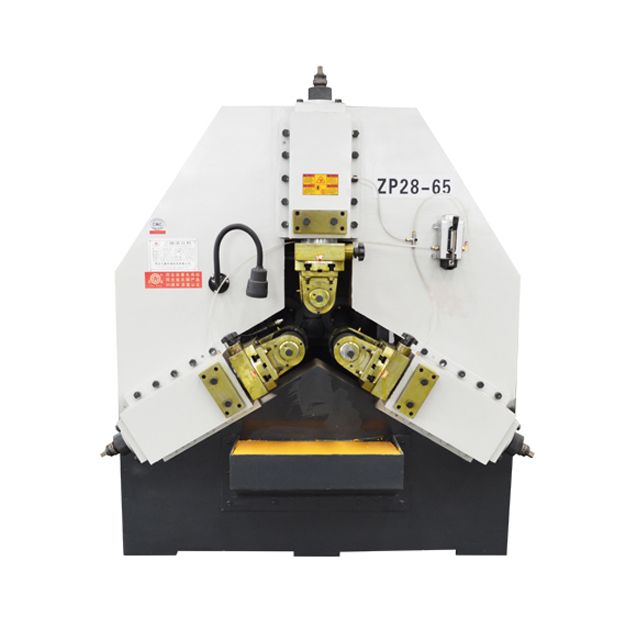
13.Can a thread rolling machines parts hs code Create Threads with Different Tolerances?
Yes, a thread rolling machine can create threads with different tolerances. The machine can be adjusted to produce threads with different pitch, diameter, and depth, which ultimately affects the tolerance of the thread. The operator can also adjust the pressure and speed of the machine to achieve the desired tolerance. However, it is important to note that the accuracy and consistency of the thread rolling machine play a crucial role in achieving the desired tolerance. Regular maintenance and calibration of the machine are necessary to ensure consistent and accurate thread production.
14.What are the Main Components of a thread rolling machines parts hs code?
I have a comprehensive after -sales service system, which can pay attention to market trends in time and adjust our strategy in a timely manner.
1. Bed: The bed is the main structural component of a thread rolling machine. It provides a stable base for all other components and supports the weight of the machine.
2. Headstock: The headstock is the part of the machine that holds the workpiece and rotates it during the thread rolling process. It also houses the drive mechanism for the workpiece rotation.
3. Tailstock: The tailstock is the part of the machine that supports the other end of the workpiece and provides stability during the thread rolling process.
4. Spindle: The spindle is the rotating shaft that holds the thread rolling dies. It is driven by the headstock and rotates the workpiece during the thread rolling process.
5. Thread Rolling Dies: These are the tools that actually form the threads on the workpiece. They are made of hardened steel and come in various sizes and shapes depending on the type of thread to be rolled.
6. Feed Mechanism: The feed mechanism is responsible for moving the thread rolling dies towards and away from the workpiece. It is usually controlled by a hydraulic or mechanical system.
7. Control Panel: The control panel is where the operator can set and adjust the parameters of the thread rolling process, such as the speed, feed rate, and depth of the thread.
8. Lubrication System: Thread rolling machines require a constant supply of lubricant to reduce friction and heat during the rolling process. The lubrication system ensures that the dies and workpiece are properly lubricated.
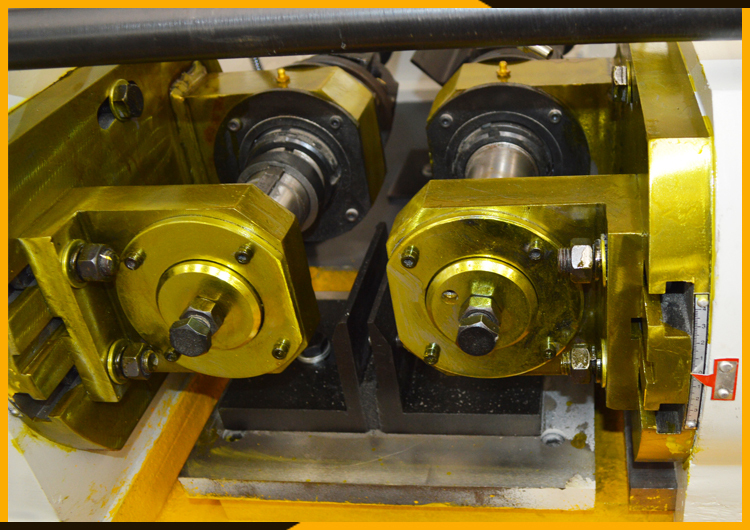
- Place of Origin:
- Video outgoing-inspection:
- Machinery Test Report:
- Marketing Type:
- Warranty of core components:
- Core Components:
- Key Selling Points:
- Applicable Industries:
- Application:
- Condition:
- Production Capacity:
- Voltage: