huide
thread rolling machine types
We focus on innovation, quality orientation, integrity philosophy sincere cooperation, and win-win strategy. We will transcend itself, continue to create value for customers and provide better technologies and best after-sales services.Please contact for further discussion and cooperation, thank you.
Product name | thread rolling machine types |
Keyword | discount thread rolling machine,what is flat die thread rolling machine,hs code for hydraulic thread rolling machine,wholesale three rollers rolling machine,thread rolling machine specification,rolling thread machine |
Place of Origin | China |
Production Capacity | 245~400/Per Min |
Power | 2.2~6kw |
Thread Dia(mm) | 2.0~4.0 |
Core Components | Motor |
Thread Length(mm) | 4~50 |
Condition | New |
Pre-Sales Service | Inquiry and consulting support. View our Factory. |
Feature | pipe nipple threading machine in its rolling pressure range of cold, the workpiece for thread, ruled, twill and other treatment; straight, helical and oblique spline gear rolling; straightening, reducing diameter, rolling and various forming rolling. |
Dimensions | 1648mm*1438mm*2031mm, (Contact us for specific information to confirm) |
Applicable Industries | Building Material Shops, etc. |
Advantages | thread rolling machine types--It can be used to process scerw and rebar.The rebar processed by the machine has the good overall mechanical.It can make the tensile strength increased by 20%-30%,the fatigue strength increased by 40%-60%,corrosion resistance increased by 50%-200%.Mechanical properties of rebar connector reached and more than international standards. |
Weight | 2517kg |
Product Description | The machine has a safe and reliable electro-hydraulic execution and control system. Each work cycle can be selected in manual, semi-automatic and automatic ways. |
terms of packing | enerally, we pack our goods in plywood cases. |
terms of paymen | T/T 30% as deposit, and 70% balance against BL copy |
Life span | 18 years (Contact us for specific information to confirm) |
After-sale service | 12 months warrantly, man-made destory will be exception. |
thread rolling machine types Advantage | We keep good quality and competitive price to ensure our customers benefit |
Packing | 2768x2233x1911mm(Contact us for specific information to confirm) |
OEM/ODM | Customization Service Provided |
Sales country | All over the world for example:Jamaica,Kenya,Bosnia and Herzegovina,British Virgin Islands,Slovenia,Belgium,Puerto Rico,Nepal |
MOQ | 7pcs(Contact us for specific information to confirm) |
Delivery time | 15-20 days for OEM, 5-7days for ready goods. |
thread rolling machine types
huide-machinery.as one of the most professional thread rolling machine types manufacturer has the advantages at:
We are the leader thread rolling machine supplier in China, also we have customers worldwide, such as America, Argentina, Brazil, Belarus, Bangladesh, Jamaica,Kenya,Bosnia and Herzegovina,British Virgin Islands,Slovenia,Belgium,Puerto Rico,Nepal, and Italy.We are factory specializing in the manufacture and export of thread rolling machine for more than 20 years, all of the production we sale are at a very best price and high quality.
We take care of our product quality, any defect of the goods, we will take responsibility. You are risk-free.And we believe that the good quality products will can give us survival, so, we always offer the top quality products to our customers, to keep them have the competitiveness in there market.
thread rolling machine types services FAQs Guide
Are you looking for a quick review guide about thread rolling machine typesservices?
An ultimate FAQ buying guide is available to help you.This guide contains all the information about all the important facts, figures, and various processes regarding thread rolling machine types services.
Let’s continue!
2.What are the Safety Precautions when Operating a thread rolling machine types?
3.How long does it take to set up and operate a thread rolling machine types?
4.What is the Typical Production Rate of a thread rolling machine types?
5.How Accurate are Threads Created by a thread rolling machine types?
6.What is the Difference Between Annular and Circular Thread Rolling?
7.What are the Main Components of a thread rolling machine types?
8.How does the thread rolling process compare to other methods such as chasing or grinding?
9.What are the Different thread rolling machine types Drive Types?
10.How Does the Thread Rolling Process Work?
11.Can a thread rolling machine types create threads on hardened materials?
12.What are the Different Types of Thread Rolling Patterns?
1.What is the Typical Lifespan of a thread rolling machine types?
The typical lifespan of a thread rolling machine can vary depending on several factors such as usage, maintenance, and quality of the machine. However, on average, a thread rolling machine can last for 10-15 years with proper care and maintenance. Some high-quality machines can even last for 20-25 years. Regular maintenance and timely repairs can also extend the lifespan of a thread rolling machine.
2.What are the Safety Precautions when Operating a thread rolling machine types?
We adhere to the principle of quality first and have a complete production quality management system and quality inspection process.
1. Wear appropriate personal protective equipment (PPE) such as safety glasses, gloves, and earplugs to protect against flying debris and noise.
2. Make sure the machine is properly grounded to prevent electrical hazards.
3. Before starting the machine, ensure that all guards and safety devices are in place and functioning properly.
4. Keep the work area clean and free of clutter to prevent tripping hazards.
5. Do not wear loose clothing or jewelry that could get caught in the machine.
6. Familiarize yourself with the machine's operating manual and follow all safety instructions.
7. Never operate the machine if you are fatigued or under the influence of drugs or alcohol.
8. Do not attempt to adjust or repair the machine while it is in operation.
9. Use the correct size and type of thread rolling dies for the material being worked on.
10. Always use a push stick or other tool to feed the material into the machine to keep your hands and fingers away from the moving parts.
11. Do not touch the rotating parts of the machine while it is in operation.
12. If the machine jams or malfunctions, turn off the power and wait for all moving parts to come to a complete stop before attempting to fix the issue.
13. Regularly inspect the machine for any signs of wear or damage and perform maintenance as recommended by the manufacturer.
14. Only trained and authorized personnel should operate the thread rolling machine.
15. In case of an emergency, know the location of the emergency stop button and how to use it.
3.How long does it take to set up and operate a thread rolling machine types?
We should enjoy a good reputation in the industry, and we can increase the added value of the products of cooperative customers through technological innovation.
The time it takes to set up and operate a thread rolling machine can vary depending on the specific machine and the experience of the operator. Generally, it can take anywhere from 15 minutes to an hour to set up the machine, including adjusting the dies and making any necessary adjustments. Once the machine is set up, the actual operation can take anywhere from a few seconds to a few minutes, depending on the length and complexity of the thread being rolled. With practice and experience, an operator can become more efficient and reduce the setup and operation time.
4.What is the Typical Production Rate of a thread rolling machine types?
The typical production rate of a thread rolling machine can vary depending on the type and size of the machine, as well as the material being rolled. However, on average, a thread rolling machine can produce between 60 to 120 parts per minute. Some high-speed machines can even produce up to 300 parts per minute.

5.How Accurate are Threads Created by a thread rolling machine types?
We are centered on customers and always pay attention to customers' needs for thread rolling machine types products.
Threads created by a thread rolling machine are highly accurate and precise. This is because thread rolling is a cold forming process that uses pressure to deform the material into the desired thread shape. This results in a thread with a smooth surface and consistent dimensions.
The accuracy of threads created by a thread rolling machine depends on several factors such as the quality of the machine, the material being rolled, and the skill of the operator. However, in general, thread rolling machines can produce threads with tolerances as tight as 0.0005 inches.
Compared to other methods of creating threads, such as cutting or grinding, thread rolling offers superior accuracy and consistency. This is because the material is not removed during the process, resulting in a stronger and more precise thread.
In addition, thread rolling machines are designed to produce threads with high repeatability, meaning that each thread produced will be nearly identical to the previous one. This makes them ideal for high-volume production of threaded parts.
Overall, the accuracy of threads created by a thread rolling machine is very high, making it a preferred method for creating threads in various industries such as automotive, aerospace, and construction.
6.What is the Difference Between Annular and Circular Thread Rolling?
We have been working hard to improve service quality and meet customer needs.
Annular and circular thread rolling are two methods used to create threads on cylindrical parts. The main difference between these two methods lies in the shape of the thread produced.
Annular thread rolling is a process in which a cylindrical part is rotated between two dies, one of which has a thread-shaped groove. As the part is rotated, the dies move together, pressing the thread-shaped groove into the surface of the part, creating a helical thread. This method produces threads with a triangular cross-section, with rounded peaks and valleys.
On the other hand, circular thread rolling is a process in which a cylindrical part is rotated between two dies, both of which have thread-shaped grooves. As the part is rotated, the dies move together, pressing the thread-shaped grooves into the surface of the part, creating a helical thread. This method produces threads with a circular cross-section, with sharp peaks and valleys.
In summary, the main difference between annular and circular thread rolling is the shape of the thread produced. Annular thread rolling produces triangular threads, while circular thread rolling produces circular threads. The choice between these two methods depends on the specific requirements of the application and the desired thread shape.
7.What are the Main Components of a thread rolling machine types?
I have a comprehensive after -sales service system, which can pay attention to market trends in time and adjust our strategy in a timely manner.
1. Bed: The bed is the main structural component of a thread rolling machine. It provides a stable base for all other components and supports the weight of the machine.
2. Headstock: The headstock is the part of the machine that holds the workpiece and rotates it during the thread rolling process. It also houses the drive mechanism for the workpiece rotation.
3. Tailstock: The tailstock is the part of the machine that supports the other end of the workpiece and provides stability during the thread rolling process.
4. Spindle: The spindle is the rotating shaft that holds the thread rolling dies. It is driven by the headstock and rotates the workpiece during the thread rolling process.
5. Thread Rolling Dies: These are the tools that actually form the threads on the workpiece. They are made of hardened steel and come in various sizes and shapes depending on the type of thread to be rolled.
6. Feed Mechanism: The feed mechanism is responsible for moving the thread rolling dies towards and away from the workpiece. It is usually controlled by a hydraulic or mechanical system.
7. Control Panel: The control panel is where the operator can set and adjust the parameters of the thread rolling process, such as the speed, feed rate, and depth of the thread.
8. Lubrication System: Thread rolling machines require a constant supply of lubricant to reduce friction and heat during the rolling process. The lubrication system ensures that the dies and workpiece are properly lubricated.
8.How does the thread rolling process compare to other methods such as chasing or grinding?
We should have a stable supply chain and logistics capabilities, and provide customers with high -quality, low -priced thread rolling machine types products.
Thread rolling is a cold forming process that uses hardened steel dies to deform the surface of a cylindrical blank, creating the desired thread profile. This process is typically used for high volume production of precision threads and offers several advantages over other methods such as chasing or grinding.
1. Faster Production Speed: Thread rolling is a high-speed process that can produce threads at a rate of up to 1000 parts per minute. This is significantly faster than chasing or grinding, which are typically slower processes.
2. Improved Thread Strength: The cold forming process of thread rolling results in a work-hardened surface that is stronger and more durable than threads produced by chasing or grinding. This makes thread rolling ideal for applications that require high strength and reliability.
3. Better Surface Finish: Thread rolling produces a smooth and precise thread surface, which is important for applications that require a tight fit or smooth movement. Chasing and grinding can result in rougher surfaces that may require additional finishing processes.
4. Cost-Effective: Thread rolling is a cost-effective process, especially for high volume production. The use of hardened steel dies also makes it a more durable and long-lasting method compared to chasing or grinding, which may require frequent replacement of tools.
5. Versatility: Thread rolling can be used to produce a wide range of thread sizes and profiles, making it a versatile process for various applications. It can also be used on a variety of materials, including steel, aluminum, and plastic.
In comparison, chasing and grinding are more suitable for smaller production runs or for repairing damaged threads. They also require more skilled labor and may result in higher costs for tooling and setup. However, they may be more suitable for producing specialized or non-standard thread profiles.
Overall, thread rolling offers a faster, more cost-effective, and versatile method for producing high-quality threads, making it a preferred choice for many industrial applications.
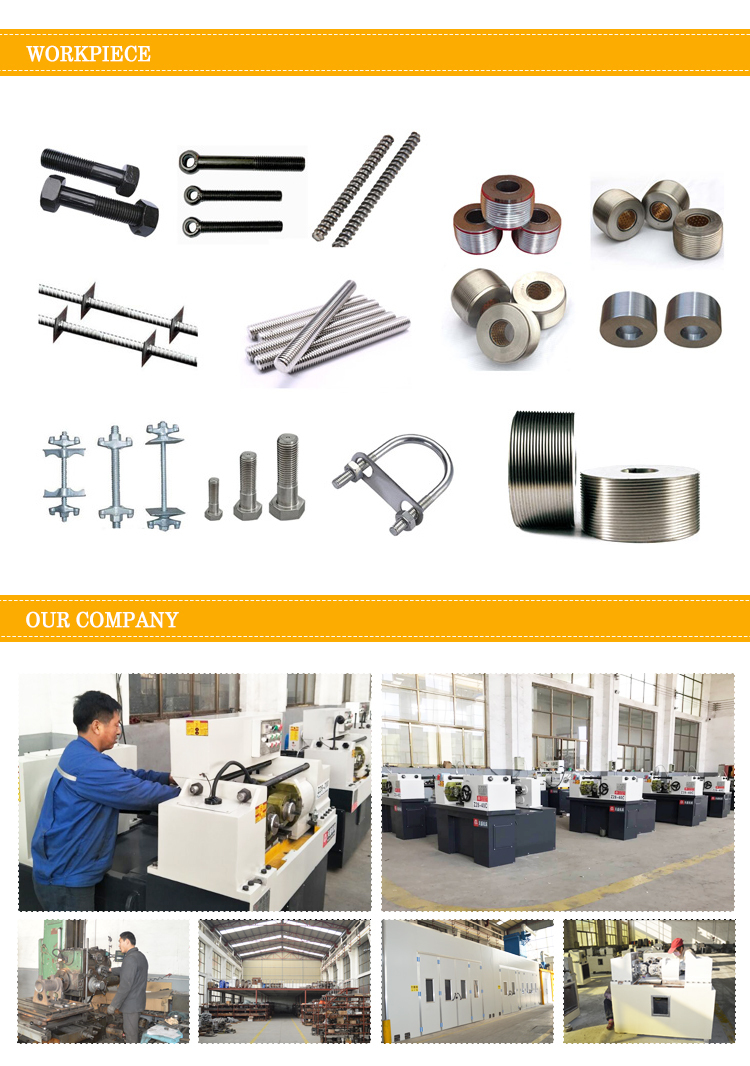
9.What are the Different thread rolling machine types Drive Types?
Being one of the top thread rolling machine types manufacturers in China, We attach great importance to this detail.
1. Mechanical Drive: This type of drive uses a motor and gears to power the thread rolling machine. The motor drives the gears, which in turn rotate the dies to create the threads.
2. Hydraulic Drive: In this type of drive, a hydraulic pump is used to power the thread rolling machine. The pump creates pressure, which is used to rotate the dies and create the threads.
3. Pneumatic Drive: A pneumatic drive uses compressed air to power the thread rolling machine. The air is used to rotate the dies and create the threads.
4. Servo Drive: This type of drive uses a servo motor to power the thread rolling machine. The motor is controlled by a computer, which allows for precise control over the rotation of the dies.
5. Electric Drive: An electric drive uses an electric motor to power the thread rolling machine. The motor is connected to the dies and rotates them to create the threads.
6. Direct Drive: In this type of drive, the dies are directly connected to the motor without any gears or other components. This allows for a more efficient transfer of power and faster thread rolling.
7. Belt Drive: A belt drive uses a belt to transfer power from the motor to the dies. This type of drive is commonly used in smaller thread rolling machines.
8. Chain Drive: Similar to a belt drive, a chain drive uses a chain to transfer power from the motor to the dies. This type of drive is commonly used in larger thread rolling machines.
10.How Does the Thread Rolling Process Work?
We attach importance to the innovation ability and team spirit of employees, have advanced R & D facilities and laboratories, and have a good quality management system.
The thread rolling process is a cold forming process used to create external threads on a workpiece. It involves pressing a hardened steel die onto the surface of the workpiece, causing the material to flow and form the desired thread shape.
The process begins with a blank workpiece, typically a cylindrical rod or bar, which is fed into the thread rolling machine. The machine consists of two dies, an upper and a lower die, which are mounted on parallel spindles and rotate in opposite directions.
The upper die is stationary, while the lower die is adjustable and can be moved up and down to accommodate different thread sizes. The dies are also equipped with thread profiles that correspond to the desired thread shape.
As the workpiece is fed between the two dies, it is gripped and held in place by a set of rollers. The rollers apply pressure to the workpiece, forcing it to deform and flow into the thread profile of the dies.
The dies then rotate, causing the material to be displaced and formed into the desired thread shape. The pressure and rotation of the dies continue until the thread is fully formed.
Once the thread is formed, the dies retract, and the workpiece is released. The thread is then checked for accuracy using gauges and other measuring tools.
The thread rolling process is highly efficient and can produce threads at a much faster rate than traditional cutting methods. It also results in a stronger and more precise thread, making it a preferred method for creating high-quality threads in mass production.
11.Can a thread rolling machine types create threads on hardened materials?
Our company has many years of thread rolling machine types experience and expertise.
Yes, a thread rolling machine can create threads on hardened materials.
The process of thread rolling involves pressing a hardened steel die onto the surface of the material, which displaces the material and forms the threads. This process is suitable for creating threads on a wide range of materials, including hardened materials such as stainless steel, titanium, and hardened steel. However, the hardness of the material may affect the speed and efficiency of the thread rolling process. It is important to use the appropriate die and machine settings for the specific material being threaded to ensure the best results.
12.What are the Different Types of Thread Rolling Patterns?
We have a good reputation and image in the industry. The quality and price advantage of thread rolling machine types products is an important factor in our hard overseas market.
1. Straight Thread Rolling: This is the most common type of thread rolling pattern, where the threads are rolled in a straight line along the length of the workpiece.
2. Helical Thread Rolling: In this pattern, the threads are rolled in a helical or spiral shape around the workpiece. This type of pattern is commonly used for creating threads on screws and bolts.
3. Diamond Thread Rolling: In this pattern, the threads are rolled in a diamond shape, with each thread intersecting at a 60-degree angle. This pattern is commonly used for creating threads on fasteners and fittings.
4. Knurling Thread Rolling: This pattern is similar to diamond thread rolling, but the threads are rolled in a knurled pattern, creating a rough surface for better grip. This type of pattern is commonly used for creating threads on handles and knobs.
5. Worm Thread Rolling: In this pattern, the threads are rolled in a spiral shape, similar to a worm gear. This type of pattern is commonly used for creating threads on gears and other mechanical components.
6. Acme Thread Rolling: This pattern is characterized by a trapezoidal shape, with flat tops and bottoms and angled sides. It is commonly used for creating threads on lead screws and other power transmission components.
7. Buttress Thread Rolling: This pattern is similar to Acme thread rolling, but with one side of the thread at a steeper angle. It is commonly used for creating threads on heavy-duty applications, such as in the oil and gas industry.
8. Square Thread Rolling: In this pattern, the threads are rolled in a square shape, with sharp corners. It is commonly used for creating threads on precision instruments and machinery.
9. Round Thread Rolling: This pattern is similar to square thread rolling, but with rounded corners. It is commonly used for creating threads on delicate materials, such as plastics and soft metals.
10. Multiple Thread Rolling: In this pattern, multiple threads are rolled simultaneously, creating a faster and more efficient process. It is commonly used for creating threads on high-volume production runs.
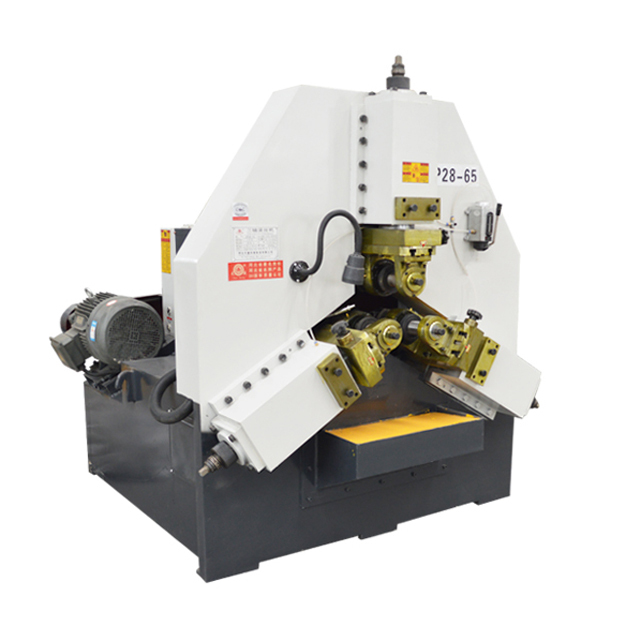
- Place of Origin:
- Video outgoing-inspection:
- Machinery Test Report:
- Marketing Type:
- Warranty of core components:
- Core Components:
- Key Selling Points:
- Applicable Industries:
- Application:
- Condition:
- Production Capacity:
- Voltage: