huide
thread rolling machine for bolt
Our target customers are all customers from all over world( Belize,Italy,Algeria,Clipperton Island,Haiti,Finland,Falkland Islands,Niger,North America, America, Africa and Oceania) who need our product.
We focus on customer focus--Identify customer needs with sincere and professional communication, Strictly control the production process to provide customers with high-quality products, professional technology and after-sales service to provide customers with the best-sales service and guarantee.
Product name | thread rolling machine for bolt |
Keyword | automatic thread rolling machine video,circular thread rolling machine,thread rolling machine manual,thread rolling machine parts,china straight thread rolling machine,thread rolling machine price,thread rolling machine video die flat hex spacer |
Place of Origin | China |
Production Capacity | 299~400/Per Min |
Power | 2.2~6kw |
Thread Dia(mm) | 2.0~4.0 |
Thread Length(mm) | 10~50 |
Feature | pipe nipple threading machine in its rolling pressure range of cold, the workpiece for thread, ruled, twill and other treatment; straight, helical and oblique spline gear rolling; straightening, reducing diameter, rolling and various forming rolling. |
Dimensions | 1581mm*1419mm*1814mm, (Contact us for specific information to confirm) |
Applicable Industries | Building Material Shops, etc. |
Color | purple or customized |
Weight | 2788kg |
Product Description | The machine has a safe and reliable electro-hydraulic execution and control system. Each work cycle can be selected in manual, semi-automatic and automatic ways. |
terms of packing | enerally, we pack our goods in plywood cases. |
terms of paymen | T/T 30% as deposit, and 70% balance against BL copy |
Life span | 14 years (Contact us for specific information to confirm) |
After-sale service | 12 months warrantly, man-made destory will be exception. |
thread rolling machine for bolt Advantage | We keep good quality and competitive price to ensure our customers benefit |
Packing | 2212x2844x2413mm(Contact us for specific information to confirm) |
OEM/ODM | Customization Service Provided |
Sales country | All over the world for example:Belize,Italy,Algeria,Clipperton Island,Haiti,Finland,Falkland Islands,Niger |
MOQ | 3pcs(Contact us for specific information to confirm) |
Delivery time | 15-20 days for OEM, 5-7days for ready goods. |
thread rolling machine for bolt
huide-machinery.as one of the most professional thread rolling machine for bolt manufacturer has the advantages at:
We are the leader thread rolling machine supplier in China, also we have customers worldwide, such as America, Argentina, Brazil, Belarus, Bangladesh, Belize,Italy,Algeria,Clipperton Island,Haiti,Finland,Falkland Islands,Niger, and Italy.We are factory specializing in the manufacture and export of thread rolling machine for more than 20 years, all of the production we sale are at a very best price and high quality.
We take care of our product quality, any defect of the goods, we will take responsibility. You are risk-free.And we believe that the good quality products will can give us survival, so, we always offer the top quality products to our customers, to keep them have the competitiveness in there market.
thread rolling machine for bolt services FAQs Guide
Are you looking for a quick review guide about thread rolling machine for boltservices?
An ultimate FAQ buying guide is available to help you.This guide contains all the information about all the important facts, figures, and various processes regarding thread rolling machine for bolt services.
Let’s continue!
2.Can a thread rolling machine for bolt Create Threads on Hard Materials?
3.What are the Different thread rolling machine for bolt Drive Types?
4.What is the Difference Between Annular and Circular Thread Rolling?
5.Is the thread rolling process more cost-effective than traditional machining methods?
6. If the machine get damaged, what can I do ?
7.What is the maximum thread size that can be rolled with this machine?
8.How Does the Size of a thread rolling machine for bolt Affect Production?
9.What materials can be used with a thread rolling machine for bolt?
10.How does the thread rolling process compare to other methods such as chasing or grinding?
11.How Accurate are Threads Created by a thread rolling machine for bolt?
12.What are the main features of a high-quality thread rolling machine for bolt?
13.What is the difference between thread rolling and thread cutting?
1.What safety precautions should be taken when operating a thread rolling machine for bolt?
We pay attention to user experience and product quality, and provide the best product quality and lowest production cost for cooperative customers.
1. Wear appropriate personal protective equipment (PPE) such as safety glasses, gloves, and earplugs.
2. Make sure the machine is properly grounded to prevent electrical hazards.
3. Keep the work area clean and free of clutter to avoid tripping hazards.
4. Familiarize yourself with the machine's operating manual and follow all safety instructions.
5. Do not wear loose clothing or jewelry that could get caught in the machine.
6. Always use the correct size and type of dies for the thread being rolled.
7. Do not touch the rotating parts of the machine while it is in operation.
8. Keep your hands and fingers away from the die area and feeding mechanism.
9. Do not attempt to adjust or repair the machine while it is running.
10. Use a push stick or other tool to feed the material into the machine to avoid hand injuries.
11. Do not overload the machine with excessive material.
12. Regularly inspect the machine for any signs of wear or damage and perform maintenance as needed.
13. If the machine malfunctions or makes unusual noises, stop the operation immediately and consult a qualified technician.
14. Always turn off the machine and disconnect the power before performing any maintenance or cleaning.
15. Train all operators on the safe operation of the machine and ensure they follow all safety precautions.
2.Can a thread rolling machine for bolt Create Threads on Hard Materials?
Yes, a thread rolling machine can create threads on hard materials. Thread rolling is a cold forming process that uses pressure to deform the material and create threads. This process is suitable for both soft and hard materials, including steel, stainless steel, titanium, and other alloys. The pressure applied by the thread rolling machine can be adjusted to accommodate the hardness of the material, ensuring that the threads are formed without damaging the material. Additionally, thread rolling can produce stronger and more precise threads compared to other methods such as cutting or tapping, making it a preferred method for creating threads on hard materials.
3.What are the Different thread rolling machine for bolt Drive Types?
Being one of the top thread rolling machine for bolt manufacturers in China, We attach great importance to this detail.
1. Mechanical Drive: This type of drive uses a motor and gears to power the thread rolling machine. The motor drives the gears, which in turn rotate the dies to create the threads.
2. Hydraulic Drive: In this type of drive, a hydraulic pump is used to power the thread rolling machine. The pump creates pressure, which is used to rotate the dies and create the threads.
3. Pneumatic Drive: A pneumatic drive uses compressed air to power the thread rolling machine. The air is used to rotate the dies and create the threads.
4. Servo Drive: This type of drive uses a servo motor to power the thread rolling machine. The motor is controlled by a computer, which allows for precise control over the rotation of the dies.
5. Electric Drive: An electric drive uses an electric motor to power the thread rolling machine. The motor is connected to the dies and rotates them to create the threads.
6. Direct Drive: In this type of drive, the dies are directly connected to the motor without any gears or other components. This allows for a more efficient transfer of power and faster thread rolling.
7. Belt Drive: A belt drive uses a belt to transfer power from the motor to the dies. This type of drive is commonly used in smaller thread rolling machines.
8. Chain Drive: Similar to a belt drive, a chain drive uses a chain to transfer power from the motor to the dies. This type of drive is commonly used in larger thread rolling machines.
4.What is the Difference Between Annular and Circular Thread Rolling?
We have been working hard to improve service quality and meet customer needs.
Annular and circular thread rolling are two methods used to create threads on cylindrical parts. The main difference between these two methods lies in the shape of the thread produced.
Annular thread rolling is a process in which a cylindrical part is rotated between two dies, one of which has a thread-shaped groove. As the part is rotated, the dies move together, pressing the thread-shaped groove into the surface of the part, creating a helical thread. This method produces threads with a triangular cross-section, with rounded peaks and valleys.
On the other hand, circular thread rolling is a process in which a cylindrical part is rotated between two dies, both of which have thread-shaped grooves. As the part is rotated, the dies move together, pressing the thread-shaped grooves into the surface of the part, creating a helical thread. This method produces threads with a circular cross-section, with sharp peaks and valleys.
In summary, the main difference between annular and circular thread rolling is the shape of the thread produced. Annular thread rolling produces triangular threads, while circular thread rolling produces circular threads. The choice between these two methods depends on the specific requirements of the application and the desired thread shape.
5.Is the thread rolling process more cost-effective than traditional machining methods?
We are a new thread rolling machine for bolt manufacturer.
Yes, the thread rolling process is generally more cost-effective than traditional machining methods for producing threads. This is because thread rolling is a faster and more efficient process that requires less material and labor compared to traditional machining methods such as cutting or grinding. Additionally, thread rolling produces stronger and more precise threads, reducing the need for additional finishing processes.
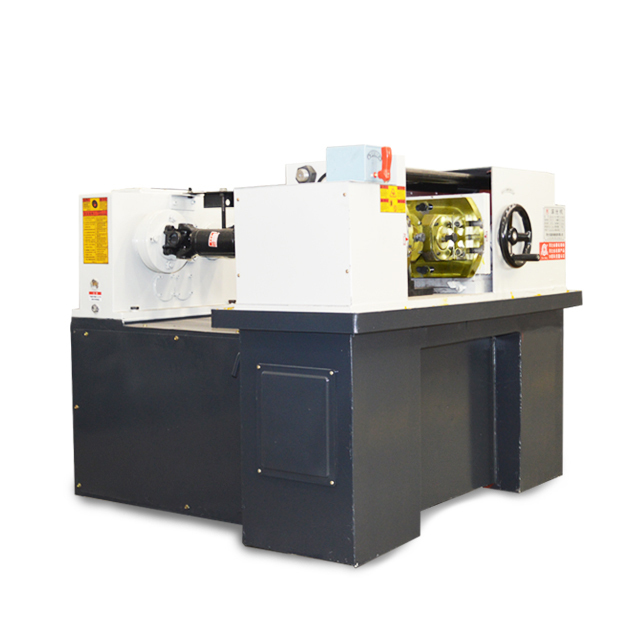
6. If the machine get damaged, what can I do ?
In the guarantee time (15 months) , we will send the spare parts to you for free and provide the technical consultant for anytime. If more terrible, we can send our engineers to your factory. We will provide same good after-sale service as the pre-sale service. For any of your questions, we will reply within 12 hours.
7.What is the maximum thread size that can be rolled with this machine?
As one of the top thread rolling machine for bolt manufacturers in China, we take this very seriously.
The maximum thread size that can be rolled with this machine depends on the specific model and specifications of the machine. It is best to consult the manufacturer or the machine's manual for the exact maximum thread size.
8.How Does the Size of a thread rolling machine for bolt Affect Production?
We actively participate in the thread rolling machine for bolt industry associations and organization activities. The corporate social responsibility performed well, and the focus of brand building and promotion
The size of a thread rolling machine can have a significant impact on production in several ways:
1. Capacity: The size of a thread rolling machine determines its capacity, i.e. the maximum size and length of the threads it can produce. A larger machine will have a higher capacity, allowing for the production of larger and longer threads. This can increase production by reducing the need for multiple setups or machine changes.
2. Speed: Generally, larger thread rolling machines have higher production speeds compared to smaller ones. This is because they have more powerful motors and can handle larger workpieces, resulting in faster thread rolling cycles. This can significantly increase production output.
3. Versatility: Smaller thread rolling machines are typically designed for specific thread sizes and types, while larger machines can handle a wider range of thread sizes and types. This versatility allows for the production of a variety of threads without the need for multiple machines, saving time and increasing production efficiency.
4. Setup and changeover time: Larger thread rolling machines often have more advanced features and automation, making setup and changeover between different thread sizes and types faster and more efficient. This reduces downtime and increases production output.
5. Maintenance and downtime: Larger thread rolling machines are generally more robust and have a longer lifespan compared to smaller machines. This means less frequent maintenance and downtime, resulting in increased production.
In summary, the size of a thread rolling machine can affect production by increasing capacity, speed, versatility, and efficiency, while also reducing downtime and maintenance. Choosing the right size machine for your production needs is crucial for maximizing productivity and profitability.
9.What materials can be used with a thread rolling machine for bolt?
We have advanced production equipment and technology to meet the needs of customers, and can provide customers with high quality, low priced thread rolling machine for bolt products.
1. Steel: Thread rolling machines are commonly used for rolling threads on steel materials, including carbon steel, alloy steel, and stainless steel.
2. Aluminum: Aluminum is another commonly used material with thread rolling machines. It is lightweight, strong, and has good corrosion resistance, making it suitable for various applications.
3. Brass: Brass is a soft and malleable material that is often used for decorative purposes. It can also be rolled into threads using a thread rolling machine.
4. Copper: Copper is a highly conductive and ductile material that is commonly used in electrical and plumbing applications. It can also be rolled into threads using a thread rolling machine.
5. Titanium: Titanium is a strong and lightweight material that is commonly used in aerospace and medical industries. It can also be rolled into threads using a thread rolling machine.
6. Plastics: Some thread rolling machines are designed to work with plastic materials, such as nylon, PVC, and polyethylene. These materials are commonly used in the production of plastic fasteners and fittings.
7. Composite materials: Thread rolling machines can also be used to roll threads on composite materials, such as fiberglass, carbon fiber, and Kevlar. These materials are commonly used in the aerospace and automotive industries.
8. Other materials: Other materials that can be used with a thread rolling machine include bronze, cast iron, and various types of alloys. The suitability of these materials will depend on the specific machine and its capabilities.
10.How does the thread rolling process compare to other methods such as chasing or grinding?
We should have a stable supply chain and logistics capabilities, and provide customers with high -quality, low -priced thread rolling machine for bolt products.
Thread rolling is a cold forming process that uses hardened steel dies to deform the surface of a cylindrical blank, creating the desired thread profile. This process is typically used for high volume production of precision threads and offers several advantages over other methods such as chasing or grinding.
1. Faster Production Speed: Thread rolling is a high-speed process that can produce threads at a rate of up to 1000 parts per minute. This is significantly faster than chasing or grinding, which are typically slower processes.
2. Improved Thread Strength: The cold forming process of thread rolling results in a work-hardened surface that is stronger and more durable than threads produced by chasing or grinding. This makes thread rolling ideal for applications that require high strength and reliability.
3. Better Surface Finish: Thread rolling produces a smooth and precise thread surface, which is important for applications that require a tight fit or smooth movement. Chasing and grinding can result in rougher surfaces that may require additional finishing processes.
4. Cost-Effective: Thread rolling is a cost-effective process, especially for high volume production. The use of hardened steel dies also makes it a more durable and long-lasting method compared to chasing or grinding, which may require frequent replacement of tools.
5. Versatility: Thread rolling can be used to produce a wide range of thread sizes and profiles, making it a versatile process for various applications. It can also be used on a variety of materials, including steel, aluminum, and plastic.
In comparison, chasing and grinding are more suitable for smaller production runs or for repairing damaged threads. They also require more skilled labor and may result in higher costs for tooling and setup. However, they may be more suitable for producing specialized or non-standard thread profiles.
Overall, thread rolling offers a faster, more cost-effective, and versatile method for producing high-quality threads, making it a preferred choice for many industrial applications.
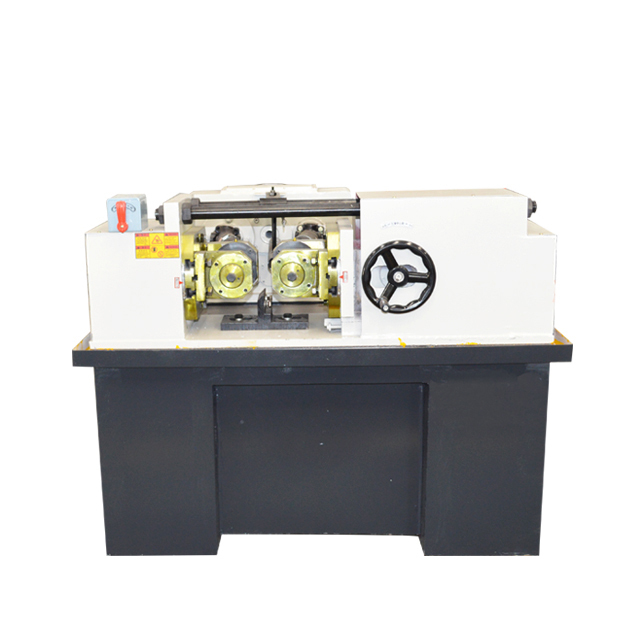
11.How Accurate are Threads Created by a thread rolling machine for bolt?
We are centered on customers and always pay attention to customers' needs for thread rolling machine for bolt products.
Threads created by a thread rolling machine are highly accurate and precise. This is because thread rolling is a cold forming process that uses pressure to deform the material into the desired thread shape. This results in a thread with a smooth surface and consistent dimensions.
The accuracy of threads created by a thread rolling machine depends on several factors such as the quality of the machine, the material being rolled, and the skill of the operator. However, in general, thread rolling machines can produce threads with tolerances as tight as 0.0005 inches.
Compared to other methods of creating threads, such as cutting or grinding, thread rolling offers superior accuracy and consistency. This is because the material is not removed during the process, resulting in a stronger and more precise thread.
In addition, thread rolling machines are designed to produce threads with high repeatability, meaning that each thread produced will be nearly identical to the previous one. This makes them ideal for high-volume production of threaded parts.
Overall, the accuracy of threads created by a thread rolling machine is very high, making it a preferred method for creating threads in various industries such as automotive, aerospace, and construction.
12.What are the main features of a high-quality thread rolling machine for bolt?
We have a wide range of thread rolling machine for bolt customer groups and establishes long -term cooperative relationships with partners. The countries we provide services include Belize,Italy,Algeria,Clipperton Island,Haiti,Finland,Falkland Islands,Niger.
1. Robust Construction: A high-quality thread rolling machine should have a sturdy and durable construction to withstand the high pressure and stress of the rolling process.
2. Precision and Accuracy: The machine should be able to produce threads with high precision and accuracy, ensuring consistent and uniform thread quality.
3. High Production Capacity: A good thread rolling machine should have a high production capacity, allowing for efficient and fast production of threaded parts.
4. Easy to Operate: The machine should have a user-friendly interface and controls, making it easy for operators to set up and operate the machine.
5. Versatility: A high-quality thread rolling machine should be able to produce a wide range of thread sizes and types, making it suitable for various applications.
6. Low Maintenance: The machine should be designed for easy maintenance, with readily available spare parts and minimal downtime for repairs.
13.What is the difference between thread rolling and thread cutting?
We have the leading technology and innovation capabilities, and attach importance to employee training and development, and provide promotion opportunities.
Thread rolling and thread cutting are two different methods used to create threads on a workpiece. The main difference between them lies in the way the threads are formed.
Thread rolling is a cold forming process in which a hardened steel die is pressed against the surface of a rotating workpiece. The pressure from the die creates the threads on the workpiece by displacing the material. This process is typically used for creating external threads on cylindrical parts, such as bolts, screws, and studs. It is a highly efficient and precise method that produces strong and accurate threads.
On the other hand, thread cutting is a machining process in which a cutting tool is used to remove material from the workpiece to create threads. The cutting tool is usually a tap or a die, and it is rotated or moved along the workpiece to cut the threads. This process is commonly used for creating internal threads on holes or external threads on shafts. It is a slower process compared to thread rolling, but it allows for more flexibility in terms of thread size and shape.
In summary, thread rolling is a cold forming process that uses pressure to create threads, while thread cutting is a machining process that uses cutting tools to remove material and create threads. Both methods have their advantages and are used in different applications depending on the requirements.
- Place of Origin:
- Video outgoing-inspection:
- Machinery Test Report:
- Marketing Type:
- Warranty of core components:
- Core Components:
- Key Selling Points:
- Applicable Industries:
- Application:
- Condition:
- Production Capacity:
- Voltage: