huide
thread rolling machine dies
We focus on innovation, quality orientation, integrity philosophy sincere cooperation, and win-win strategy. We will transcend itself, continue to create value for customers and provide better technologies and best after-sales services.Please contact for further discussion and cooperation, thank you.
Product name | thread rolling machine dies |
Keyword | nail thread rolling machine,thread rolling machine manufacturer taiwan,taiwanese thread rolling machine,rebar thread rolling machine supplier,customized high speed thread rolling machine,thread rolling machine pricelist |
Place of Origin | China |
Production Capacity | 206~400/Per Min |
Power | 2.2~6kw |
Thread Dia(mm) | 2.0~4.0 |
Thread Length(mm) | 5~50 |
Feature | pipe nipple threading machine in its rolling pressure range of cold, the workpiece for thread, ruled, twill and other treatment; straight, helical and oblique spline gear rolling; straightening, reducing diameter, rolling and various forming rolling. |
Dimensions | 1888mm*1625mm*1542mm, (Contact us for specific information to confirm) |
Applicable Industries | Automotive Manufacturing, etc. |
Color | purple or customized |
Weight | 2866kg |
Product Description | The machine has a safe and reliable electro-hydraulic execution and control system. Each work cycle can be selected in manual, semi-automatic and automatic ways. |
terms of packing | enerally, we pack our goods in plywood cases. |
terms of paymen | T/T 30% as deposit, and 70% balance against BL copy |
Life span | 17 years (Contact us for specific information to confirm) |
After-sale service | 12 months warrantly, man-made destory will be exception. |
thread rolling machine dies Advantage | We keep good quality and competitive price to ensure our customers benefit |
Packing | 2160x2524x1681mm(Contact us for specific information to confirm) |
OEM/ODM | Customization Service Provided |
Sales country | All over the world for example:Tunisia,Kyrgyzstan,India,Rwanda,Christmas Island,Grenada,Zimbabwe |
MOQ | 8pcs(Contact us for specific information to confirm) |
Delivery time | 15-20 days for OEM, 5-7days for ready goods. |
thread rolling machine dies
huide-machinery.as one of the most professional thread rolling machine dies manufacturer has the advantages at:
We are the leader thread rolling machine supplier in China, also we have customers worldwide, such as America, Argentina, Brazil, Belarus, Bangladesh, Tunisia,Kyrgyzstan,India,Rwanda,Christmas Island,Grenada,Zimbabwe, and Italy.We are factory specializing in the manufacture and export of thread rolling machine for more than 20 years, all of the production we sale are at a very best price and high quality.
We take care of our product quality, any defect of the goods, we will take responsibility. You are risk-free.And we believe that the good quality products will can give us survival, so, we always offer the top quality products to our customers, to keep them have the competitiveness in there market.
thread rolling machine dies services FAQs Guide
Are you looking for a quick review guide about thread rolling machine diesservices?
An ultimate FAQ buying guide is available to help you.This guide contains all the information about all the important facts, figures, and various processes regarding thread rolling machine dies services.
Let’s continue!
2.What are the main features of a high-quality thread rolling machine dies?
3.What are the Main Components of a thread rolling machine dies?
4.How Does the Size of a thread rolling machine dies Affect Production?
5.What is the Difference Between Annular and Circular Thread Rolling?
6.Can a thread rolling machine dies Create Internal Threads?
7.Can a thread rolling machine dies Create Threads with Different Tolerances?
8.Is the thread rolling process more cost-effective than traditional machining methods?
9.What are Some Common Defects in Threads Created by a thread rolling machine dies?
10.How does the thread rolling process compare to other methods such as chasing or grinding?
11.How can a thread rolling machine dies improve the efficiency of my production process?
12.What Quality Control Measures are Used in thread rolling machine dies Production?
13.What Types of Materials can be Used with a thread rolling machine dies?
1.What is the Typical Lifespan of a thread rolling machine dies?
The typical lifespan of a thread rolling machine can vary depending on several factors such as usage, maintenance, and quality of the machine. However, on average, a thread rolling machine can last for 10-15 years with proper care and maintenance. Some high-quality machines can even last for 20-25 years. Regular maintenance and timely repairs can also extend the lifespan of a thread rolling machine.
2.What are the main features of a high-quality thread rolling machine dies?
We have a wide range of thread rolling machine dies customer groups and establishes long -term cooperative relationships with partners. The countries we provide services include Tunisia,Kyrgyzstan,India,Rwanda,Christmas Island,Grenada,Zimbabwe.
1. Robust Construction: A high-quality thread rolling machine should have a sturdy and durable construction to withstand the high pressure and stress of the rolling process.
2. Precision and Accuracy: The machine should be able to produce threads with high precision and accuracy, ensuring consistent and uniform thread quality.
3. High Production Capacity: A good thread rolling machine should have a high production capacity, allowing for efficient and fast production of threaded parts.
4. Easy to Operate: The machine should have a user-friendly interface and controls, making it easy for operators to set up and operate the machine.
5. Versatility: A high-quality thread rolling machine should be able to produce a wide range of thread sizes and types, making it suitable for various applications.
6. Low Maintenance: The machine should be designed for easy maintenance, with readily available spare parts and minimal downtime for repairs.
3.What are the Main Components of a thread rolling machine dies?
I have a comprehensive after -sales service system, which can pay attention to market trends in time and adjust our strategy in a timely manner.
1. Bed: The bed is the main structural component of a thread rolling machine. It provides a stable base for all other components and supports the weight of the machine.
2. Headstock: The headstock is the part of the machine that holds the workpiece and rotates it during the thread rolling process. It also houses the drive mechanism for the workpiece rotation.
3. Tailstock: The tailstock is the part of the machine that supports the other end of the workpiece and provides stability during the thread rolling process.
4. Spindle: The spindle is the rotating shaft that holds the thread rolling dies. It is driven by the headstock and rotates the workpiece during the thread rolling process.
5. Thread Rolling Dies: These are the tools that actually form the threads on the workpiece. They are made of hardened steel and come in various sizes and shapes depending on the type of thread to be rolled.
6. Feed Mechanism: The feed mechanism is responsible for moving the thread rolling dies towards and away from the workpiece. It is usually controlled by a hydraulic or mechanical system.
7. Control Panel: The control panel is where the operator can set and adjust the parameters of the thread rolling process, such as the speed, feed rate, and depth of the thread.
8. Lubrication System: Thread rolling machines require a constant supply of lubricant to reduce friction and heat during the rolling process. The lubrication system ensures that the dies and workpiece are properly lubricated.
4.How Does the Size of a thread rolling machine dies Affect Production?
We actively participate in the thread rolling machine dies industry associations and organization activities. The corporate social responsibility performed well, and the focus of brand building and promotion
The size of a thread rolling machine can have a significant impact on production in several ways:
1. Capacity: The size of a thread rolling machine determines its capacity, i.e. the maximum size and length of the threads it can produce. A larger machine will have a higher capacity, allowing for the production of larger and longer threads. This can increase production by reducing the need for multiple setups or machine changes.
2. Speed: Generally, larger thread rolling machines have higher production speeds compared to smaller ones. This is because they have more powerful motors and can handle larger workpieces, resulting in faster thread rolling cycles. This can significantly increase production output.
3. Versatility: Smaller thread rolling machines are typically designed for specific thread sizes and types, while larger machines can handle a wider range of thread sizes and types. This versatility allows for the production of a variety of threads without the need for multiple machines, saving time and increasing production efficiency.
4. Setup and changeover time: Larger thread rolling machines often have more advanced features and automation, making setup and changeover between different thread sizes and types faster and more efficient. This reduces downtime and increases production output.
5. Maintenance and downtime: Larger thread rolling machines are generally more robust and have a longer lifespan compared to smaller machines. This means less frequent maintenance and downtime, resulting in increased production.
In summary, the size of a thread rolling machine can affect production by increasing capacity, speed, versatility, and efficiency, while also reducing downtime and maintenance. Choosing the right size machine for your production needs is crucial for maximizing productivity and profitability.
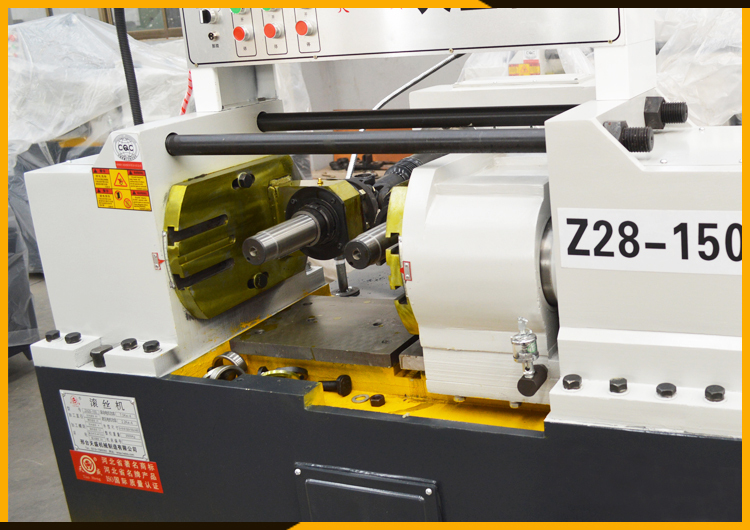
5.What is the Difference Between Annular and Circular Thread Rolling?
We have been working hard to improve service quality and meet customer needs.
Annular and circular thread rolling are two methods used to create threads on cylindrical parts. The main difference between these two methods lies in the shape of the thread produced.
Annular thread rolling is a process in which a cylindrical part is rotated between two dies, one of which has a thread-shaped groove. As the part is rotated, the dies move together, pressing the thread-shaped groove into the surface of the part, creating a helical thread. This method produces threads with a triangular cross-section, with rounded peaks and valleys.
On the other hand, circular thread rolling is a process in which a cylindrical part is rotated between two dies, both of which have thread-shaped grooves. As the part is rotated, the dies move together, pressing the thread-shaped grooves into the surface of the part, creating a helical thread. This method produces threads with a circular cross-section, with sharp peaks and valleys.
In summary, the main difference between annular and circular thread rolling is the shape of the thread produced. Annular thread rolling produces triangular threads, while circular thread rolling produces circular threads. The choice between these two methods depends on the specific requirements of the application and the desired thread shape.
6.Can a thread rolling machine dies Create Internal Threads?
We have rich industry experience and professional knowledge, and have strong competitiveness in the market.
Yes, a thread rolling machine can create internal threads. This process is known as internal thread rolling and it involves using a set of dies to form the threads on the inside of a cylindrical workpiece. This method is commonly used for creating threads on nuts, bolts, and other fasteners. Internal thread rolling is a faster and more efficient process compared to traditional methods such as tapping or cutting, and it also produces stronger and more precise threads.
7.Can a thread rolling machine dies Create Threads with Different Tolerances?
Yes, a thread rolling machine can create threads with different tolerances. The machine can be adjusted to produce threads with different pitch, diameter, and depth, which ultimately affects the tolerance of the thread. The operator can also adjust the pressure and speed of the machine to achieve the desired tolerance. However, it is important to note that the accuracy and consistency of the thread rolling machine play a crucial role in achieving the desired tolerance. Regular maintenance and calibration of the machine are necessary to ensure consistent and accurate thread production.
8.Is the thread rolling process more cost-effective than traditional machining methods?
We are a new thread rolling machine dies manufacturer.
Yes, the thread rolling process is generally more cost-effective than traditional machining methods for producing threads. This is because thread rolling is a faster and more efficient process that requires less material and labor compared to traditional machining methods such as cutting or grinding. Additionally, thread rolling produces stronger and more precise threads, reducing the need for additional finishing processes.
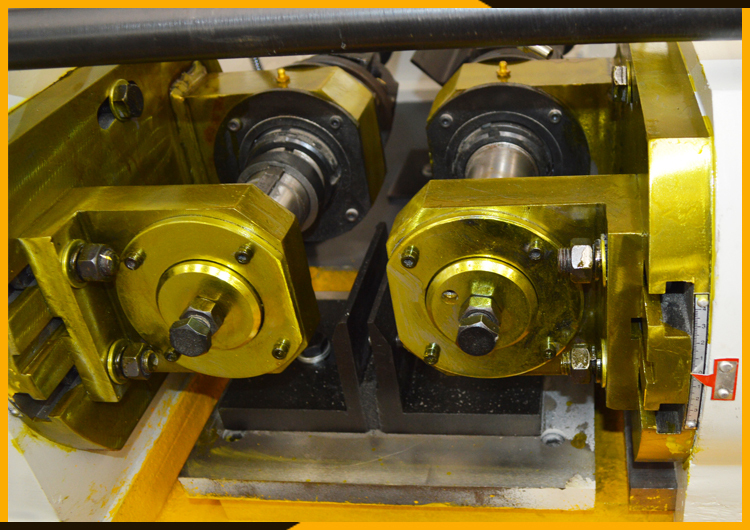
9.What are Some Common Defects in Threads Created by a thread rolling machine dies?
1. Incomplete Threads: This is a common defect where the thread is not fully formed or is missing in certain areas. This can be caused by improper alignment of the thread rolling machine or worn out dies.
2. Oversized Threads: This defect occurs when the thread is larger than the specified size. It can be caused by excessive pressure or incorrect die settings.
3. Undersized Threads: This is the opposite of oversized threads, where the thread is smaller than the specified size. It can be caused by insufficient pressure or worn out dies.
4. Tapered Threads: Tapered threads have a gradual change in diameter along the length of the thread. This can be caused by misalignment of the dies or uneven pressure during the rolling process.
5. Misaligned Threads: This defect occurs when the threads are not straight and parallel to each other. It can be caused by misalignment of the dies or improper setup of the machine.
6. Thread Flaking: Thread flaking is when small pieces of the thread break off, resulting in a rough and uneven surface. This can be caused by worn out or damaged dies.
7. Thread Cracks: Cracks in the thread can occur due to excessive pressure or improper die settings. This defect can weaken the thread and lead to failure under stress.
8. Thread Galling: Galling is a form of wear that occurs when two surfaces rub against each other. It can cause the thread to seize up and become difficult to turn.
9. Thread Stripping: This defect occurs when the thread is stripped or torn off the surface of the material. It can be caused by excessive pressure or incorrect die settings.
10. Thread Runout: Thread runout is when the thread is not concentric with the axis of the material. This can be caused by misalignment of the dies or uneven pressure during the rolling process.
10.How does the thread rolling process compare to other methods such as chasing or grinding?
We should have a stable supply chain and logistics capabilities, and provide customers with high -quality, low -priced thread rolling machine dies products.
Thread rolling is a cold forming process that uses hardened steel dies to deform the surface of a cylindrical blank, creating the desired thread profile. This process is typically used for high volume production of precision threads and offers several advantages over other methods such as chasing or grinding.
1. Faster Production Speed: Thread rolling is a high-speed process that can produce threads at a rate of up to 1000 parts per minute. This is significantly faster than chasing or grinding, which are typically slower processes.
2. Improved Thread Strength: The cold forming process of thread rolling results in a work-hardened surface that is stronger and more durable than threads produced by chasing or grinding. This makes thread rolling ideal for applications that require high strength and reliability.
3. Better Surface Finish: Thread rolling produces a smooth and precise thread surface, which is important for applications that require a tight fit or smooth movement. Chasing and grinding can result in rougher surfaces that may require additional finishing processes.
4. Cost-Effective: Thread rolling is a cost-effective process, especially for high volume production. The use of hardened steel dies also makes it a more durable and long-lasting method compared to chasing or grinding, which may require frequent replacement of tools.
5. Versatility: Thread rolling can be used to produce a wide range of thread sizes and profiles, making it a versatile process for various applications. It can also be used on a variety of materials, including steel, aluminum, and plastic.
In comparison, chasing and grinding are more suitable for smaller production runs or for repairing damaged threads. They also require more skilled labor and may result in higher costs for tooling and setup. However, they may be more suitable for producing specialized or non-standard thread profiles.
Overall, thread rolling offers a faster, more cost-effective, and versatile method for producing high-quality threads, making it a preferred choice for many industrial applications.
11.How can a thread rolling machine dies improve the efficiency of my production process?
We maintain a certain amount of R&D investment every year and continuously improve operational efficiency to provide better services to our cooperative customers.
1. Faster Production Speed: Thread rolling machines are designed to quickly and efficiently create threads on a variety of materials. This can significantly increase the speed of your production process, allowing you to produce more products in a shorter amount of time.
2. Consistent Quality: Thread rolling machines use a precise and controlled process to create threads, resulting in consistent and accurate thread dimensions. This eliminates the need for manual threading, which can be prone to human error and result in inconsistent thread quality.
3. Reduced Labor Costs: With a thread rolling machine, you can automate the threading process, reducing the need for manual labor. This can save you money on labor costs and allow your employees to focus on other tasks.
4. Versatility: Thread rolling machines can create threads on a wide range of materials, including steel, aluminum, and plastic. This versatility allows you to use the same machine for different products, reducing the need for multiple machines and saving space in your production facility.
5. Longer Tool Life: Thread rolling machines use hardened dies to create threads, which can last much longer than traditional threading tools. This means you will spend less time and money on replacing worn-out tools, further improving the efficiency of your production process.
6. Reduced Material Waste: With traditional threading methods, excess material is often removed to create the threads. This can result in a significant amount of material waste. Thread rolling machines, on the other hand, use a cold forming process that does not require material removal, reducing waste and saving you money on material costs.
7. Easy to Use: Thread rolling machines are designed to be user-friendly and easy to operate. This means that even employees with minimal training can quickly learn how to use the machine, reducing the time and resources needed for training.
8. Lower Maintenance Costs: Thread rolling machines are built to be durable and require minimal maintenance. This can save you money on maintenance costs and reduce downtime in your production process.
9. Improved Safety: Manual threading can be a hazardous task, as it involves handling sharp tools and working with rotating machinery. By automating the threading process with a thread rolling machine, you can improve the safety of your production process and reduce the risk of workplace injuries.
10. Cost Savings: Overall, the increased efficiency and productivity of using a thread rolling machine can result in significant cost savings for your production process. This can help you stay competitive in the market and increase your profitability.
12.What Quality Control Measures are Used in thread rolling machine dies Production?
1. Material Inspection: The first step in quality control is to inspect the raw materials used in the production of thread rolling machines. This includes checking the quality and specifications of the steel, bearings, gears, and other components.
2. Machine Calibration: Before starting the production process, the thread rolling machine is calibrated to ensure that it is functioning properly and producing accurate threads.
3. In-process Inspection: During the production process, regular inspections are carried out to check the dimensions, surface finish, and other critical parameters of the thread rolling machine.
4. Statistical Process Control (SPC): SPC is a method used to monitor and control the production process by collecting and analyzing data. This helps to identify any variations or defects in the production process and take corrective actions.
5. Final Inspection: Once the thread rolling machine is completed, a final inspection is carried out to ensure that it meets all the required specifications and standards.
6. Performance Testing: The thread rolling machine is tested for its performance by running it with different types of materials and thread sizes to ensure that it can produce accurate and consistent threads.
7. Quality Management System: Most manufacturers have a quality management system in place to ensure that all the processes and procedures are followed correctly and any issues are addressed promptly.
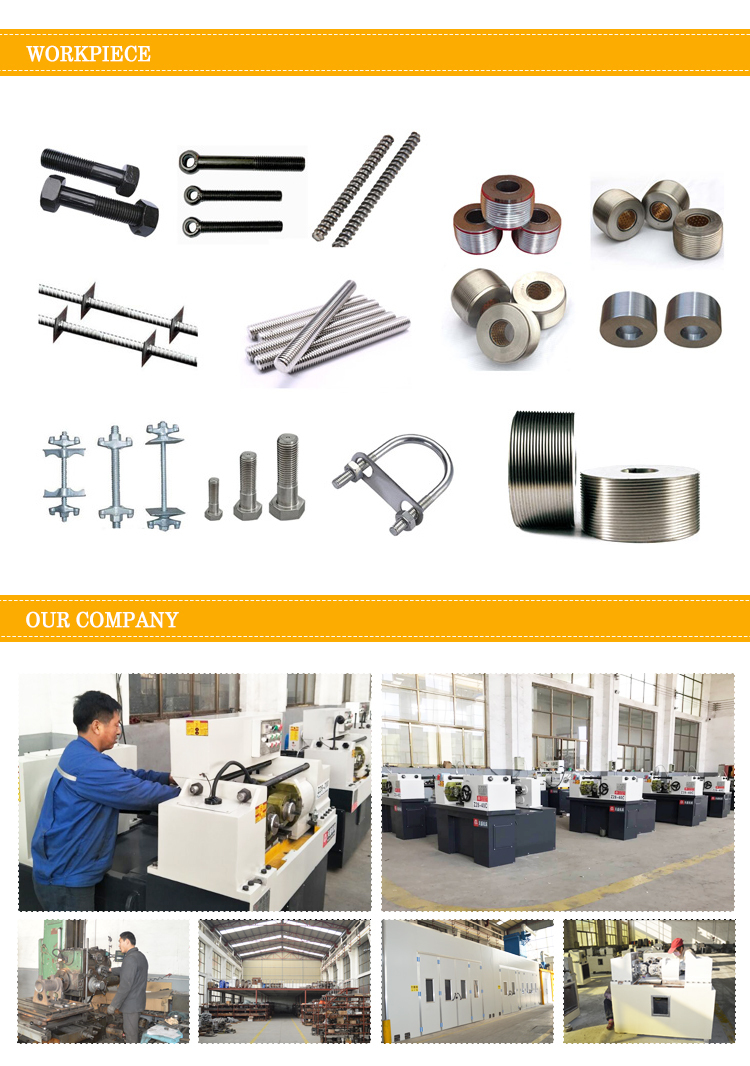
13.What Types of Materials can be Used with a thread rolling machine dies?
We continue to invest in research and development and continue to launch innovative products.
1. Metal: Thread rolling machines are primarily used for rolling threads on metal materials such as steel, aluminum, brass, and copper. These materials are commonly used in industries such as automotive, aerospace, and construction.
2. Plastic: Some thread rolling machines are also capable of rolling threads on plastic materials such as nylon, PVC, and acrylic. These materials are commonly used in industries such as electronics, medical, and consumer goods.
3. Wood: Thread rolling machines can also be used to create threads on wooden materials such as hardwood and softwood. These threads are commonly used in furniture making and woodworking industries.
4. Composite materials: Thread rolling machines can also be used to roll threads on composite materials such as carbon fiber, fiberglass, and Kevlar. These materials are commonly used in industries such as aerospace, marine, and sports equipment.
5. Rubber: Some thread rolling machines are also capable of rolling threads on rubber materials such as silicone, neoprene, and EPDM. These materials are commonly used in industries such as automotive, construction, and medical.
6. Ceramic: Thread rolling machines can also be used to create threads on ceramic materials such as porcelain, clay, and glass. These materials are commonly used in industries such as pottery, construction, and electronics.
7. Other materials: Depending on the type and capabilities of the thread rolling machine, it may also be able to roll threads on other materials such as leather, paper, and fabric. These materials are commonly used in industries such as fashion, packaging, and upholstery.
- Place of Origin:
- Video outgoing-inspection:
- Machinery Test Report:
- Marketing Type:
- Warranty of core components:
- Core Components:
- Key Selling Points:
- Applicable Industries:
- Application:
- Condition:
- Production Capacity:
- Voltage: