huide
thread rolling and screw machine
Thanks to perfect management, advanced technology, reliable quality and first-class service, international CE certification, IS09001, 2015 quality system certification and coat rack appearance patent certification.
Product name | thread rolling and screw machine |
Keyword | taiwanese thread rolling machine,old thread rolling machine,flat thread rolling dies machine,hydraulic thread rolling machine,thread rolling machine operation manual,cylindrical thread rolling machine,threaded rod thread rolling machine |
Place of Origin | China |
Production Capacity | 246~400/Per Min |
Power | 2.2~6kw |
Thread Dia(mm) | 2.0~4.0 |
Core Components | Motor |
Thread Length(mm) | 6~50 |
Condition | New |
Pre-Sales Service | Inquiry and consulting support. View our Factory. |
Feature | pipe nipple threading machine in its rolling pressure range of cold, the workpiece for thread, ruled, twill and other treatment; straight, helical and oblique spline gear rolling; straightening, reducing diameter, rolling and various forming rolling. |
Dimensions | 1633mm*1674mm*1940mm, (Contact us for specific information to confirm) |
Applicable Industries | Construction works , etc. |
Advantages | thread rolling and screw machine--It can be used to process scerw and rebar.The rebar processed by the machine has the good overall mechanical.It can make the tensile strength increased by 20%-30%,the fatigue strength increased by 40%-60%,corrosion resistance increased by 50%-200%.Mechanical properties of rebar connector reached and more than international standards. |
Weight | 2369kg |
Product Description | The machine has a safe and reliable electro-hydraulic execution and control system. Each work cycle can be selected in manual, semi-automatic and automatic ways. |
terms of packing | enerally, we pack our goods in plywood cases. |
terms of paymen | T/T 30% as deposit, and 70% balance against BL copy |
Life span | 12 years (Contact us for specific information to confirm) |
After-sale service | 12 months warrantly, man-made destory will be exception. |
thread rolling and screw machine Advantage | We keep good quality and competitive price to ensure our customers benefit |
Packing | 2250x2428x2324mm(Contact us for specific information to confirm) |
OEM/ODM | Customization Service Provided |
Sales country | All over the world for example:Antigua and Barbuda,Spain,Luxembourg,Juan de Nova Island,Switzerland,Gambia,Saint Helena,Estonia,Israel |
MOQ | 3pcs(Contact us for specific information to confirm) |
Delivery time | 15-20 days for OEM, 5-7days for ready goods. |
thread rolling and screw machine
huide-machinery.as one of the most professional thread rolling and screw machine manufacturer has the advantages at:
We are the leader thread rolling machine supplier in China, also we have customers worldwide, such as America, Argentina, Brazil, Belarus, Bangladesh, Antigua and Barbuda,Spain,Luxembourg,Juan de Nova Island,Switzerland,Gambia,Saint Helena,Estonia,Israel, and Italy.We are factory specializing in the manufacture and export of thread rolling machine for more than 20 years, all of the production we sale are at a very best price and high quality.
We take care of our product quality, any defect of the goods, we will take responsibility. You are risk-free.And we believe that the good quality products will can give us survival, so, we always offer the top quality products to our customers, to keep them have the competitiveness in there market.
thread rolling and screw machine services FAQs Guide
Are you looking for a quick review guide about thread rolling and screw machineservices?
An ultimate FAQ buying guide is available to help you.This guide contains all the information about all the important facts, figures, and various processes regarding thread rolling and screw machine services.
Let’s continue!
2.What are the Different Types of Thread Rolling Patterns?
3.What safety precautions should be taken when operating a thread rolling and screw machine?
4.How can a thread rolling and screw machine improve the efficiency of my production process?
5.Can a thread rolling and screw machine be Automated?
6.Is the thread rolling process more cost-effective than traditional machining methods?
7.Can a thread rolling and screw machine create threads on hardened materials?
8.What is a thread rolling and screw machine and how does it work?
1.What is the Typical Lifespan of a thread rolling and screw machine?
The typical lifespan of a thread rolling machine can vary depending on several factors such as usage, maintenance, and quality of the machine. However, on average, a thread rolling machine can last for 10-15 years with proper care and maintenance. Some high-quality machines can even last for 20-25 years. Regular maintenance and timely repairs can also extend the lifespan of a thread rolling machine.
2.What are the Different Types of Thread Rolling Patterns?
We have a good reputation and image in the industry. The quality and price advantage of thread rolling and screw machine products is an important factor in our hard overseas market.
1. Straight Thread Rolling: This is the most common type of thread rolling pattern, where the threads are rolled in a straight line along the length of the workpiece.
2. Helical Thread Rolling: In this pattern, the threads are rolled in a helical or spiral shape around the workpiece. This type of pattern is commonly used for creating threads on screws and bolts.
3. Diamond Thread Rolling: In this pattern, the threads are rolled in a diamond shape, with each thread intersecting at a 60-degree angle. This pattern is commonly used for creating threads on fasteners and fittings.
4. Knurling Thread Rolling: This pattern is similar to diamond thread rolling, but the threads are rolled in a knurled pattern, creating a rough surface for better grip. This type of pattern is commonly used for creating threads on handles and knobs.
5. Worm Thread Rolling: In this pattern, the threads are rolled in a spiral shape, similar to a worm gear. This type of pattern is commonly used for creating threads on gears and other mechanical components.
6. Acme Thread Rolling: This pattern is characterized by a trapezoidal shape, with flat tops and bottoms and angled sides. It is commonly used for creating threads on lead screws and other power transmission components.
7. Buttress Thread Rolling: This pattern is similar to Acme thread rolling, but with one side of the thread at a steeper angle. It is commonly used for creating threads on heavy-duty applications, such as in the oil and gas industry.
8. Square Thread Rolling: In this pattern, the threads are rolled in a square shape, with sharp corners. It is commonly used for creating threads on precision instruments and machinery.
9. Round Thread Rolling: This pattern is similar to square thread rolling, but with rounded corners. It is commonly used for creating threads on delicate materials, such as plastics and soft metals.
10. Multiple Thread Rolling: In this pattern, multiple threads are rolled simultaneously, creating a faster and more efficient process. It is commonly used for creating threads on high-volume production runs.
3.What safety precautions should be taken when operating a thread rolling and screw machine?
We pay attention to user experience and product quality, and provide the best product quality and lowest production cost for cooperative customers.
1. Wear appropriate personal protective equipment (PPE) such as safety glasses, gloves, and earplugs.
2. Make sure the machine is properly grounded to prevent electrical hazards.
3. Keep the work area clean and free of clutter to avoid tripping hazards.
4. Familiarize yourself with the machine's operating manual and follow all safety instructions.
5. Do not wear loose clothing or jewelry that could get caught in the machine.
6. Always use the correct size and type of dies for the thread being rolled.
7. Do not touch the rotating parts of the machine while it is in operation.
8. Keep your hands and fingers away from the die area and feeding mechanism.
9. Do not attempt to adjust or repair the machine while it is running.
10. Use a push stick or other tool to feed the material into the machine to avoid hand injuries.
11. Do not overload the machine with excessive material.
12. Regularly inspect the machine for any signs of wear or damage and perform maintenance as needed.
13. If the machine malfunctions or makes unusual noises, stop the operation immediately and consult a qualified technician.
14. Always turn off the machine and disconnect the power before performing any maintenance or cleaning.
15. Train all operators on the safe operation of the machine and ensure they follow all safety precautions.
4.How can a thread rolling and screw machine improve the efficiency of my production process?
We maintain a certain amount of R&D investment every year and continuously improve operational efficiency to provide better services to our cooperative customers.
1. Faster Production Speed: Thread rolling machines are designed to quickly and efficiently create threads on a variety of materials. This can significantly increase the speed of your production process, allowing you to produce more products in a shorter amount of time.
2. Consistent Quality: Thread rolling machines use a precise and controlled process to create threads, resulting in consistent and accurate thread dimensions. This eliminates the need for manual threading, which can be prone to human error and result in inconsistent thread quality.
3. Reduced Labor Costs: With a thread rolling machine, you can automate the threading process, reducing the need for manual labor. This can save you money on labor costs and allow your employees to focus on other tasks.
4. Versatility: Thread rolling machines can create threads on a wide range of materials, including steel, aluminum, and plastic. This versatility allows you to use the same machine for different products, reducing the need for multiple machines and saving space in your production facility.
5. Longer Tool Life: Thread rolling machines use hardened dies to create threads, which can last much longer than traditional threading tools. This means you will spend less time and money on replacing worn-out tools, further improving the efficiency of your production process.
6. Reduced Material Waste: With traditional threading methods, excess material is often removed to create the threads. This can result in a significant amount of material waste. Thread rolling machines, on the other hand, use a cold forming process that does not require material removal, reducing waste and saving you money on material costs.
7. Easy to Use: Thread rolling machines are designed to be user-friendly and easy to operate. This means that even employees with minimal training can quickly learn how to use the machine, reducing the time and resources needed for training.
8. Lower Maintenance Costs: Thread rolling machines are built to be durable and require minimal maintenance. This can save you money on maintenance costs and reduce downtime in your production process.
9. Improved Safety: Manual threading can be a hazardous task, as it involves handling sharp tools and working with rotating machinery. By automating the threading process with a thread rolling machine, you can improve the safety of your production process and reduce the risk of workplace injuries.
10. Cost Savings: Overall, the increased efficiency and productivity of using a thread rolling machine can result in significant cost savings for your production process. This can help you stay competitive in the market and increase your profitability.
5.Can a thread rolling and screw machine be Automated?
We focus on teamwork and communication to achieve common goals, We attach great importance to this detail.
Yes, a thread rolling machine can be automated. Automation can be achieved through the use of computer numerical control (CNC) technology, which allows for precise and repeatable control of the machine's movements and operations. This can greatly increase the efficiency and productivity of the thread rolling process, as well as reduce the potential for human error. Additionally, some thread rolling machines may also have built-in automation features such as automatic thread length measurement and adjustment, automatic lubrication systems, and automatic tool change capabilities.
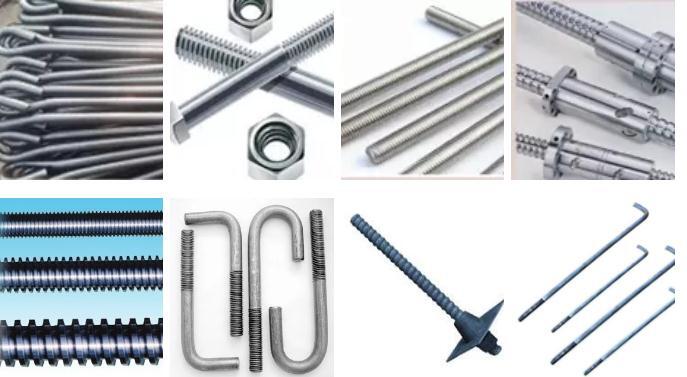
6.Is the thread rolling process more cost-effective than traditional machining methods?
We are a new thread rolling and screw machine manufacturer.
Yes, the thread rolling process is generally more cost-effective than traditional machining methods for producing threads. This is because thread rolling is a faster and more efficient process that requires less material and labor compared to traditional machining methods such as cutting or grinding. Additionally, thread rolling produces stronger and more precise threads, reducing the need for additional finishing processes.
7.Can a thread rolling and screw machine create threads on hardened materials?
Our company has many years of thread rolling and screw machine experience and expertise.
Yes, a thread rolling machine can create threads on hardened materials.
The process of thread rolling involves pressing a hardened steel die onto the surface of the material, which displaces the material and forms the threads. This process is suitable for creating threads on a wide range of materials, including hardened materials such as stainless steel, titanium, and hardened steel. However, the hardness of the material may affect the speed and efficiency of the thread rolling process. It is important to use the appropriate die and machine settings for the specific material being threaded to ensure the best results.
8.What is a thread rolling and screw machine and how does it work?
We pay attention to the introduction and training of talents, scientifically regulate the management system, and focus on cultural construction and team cohesion.
A thread rolling machine is a type of machine used to create threads on a workpiece. It works by pressing a hardened steel die onto the surface of the workpiece, which then displaces the material to form the thread shape.
The machine consists of a fixed and a moving die, with the workpiece being placed between them. The dies have a thread profile that matches the desired thread shape. The workpiece is then rotated while the dies are pressed against it, causing the material to be displaced and form the thread.
The thread rolling process is a cold forming process, meaning that no heat is applied to the workpiece. This results in a stronger and more precise thread compared to other methods such as cutting or grinding.
Thread rolling machines are commonly used in the production of screws, bolts, and other threaded components. They can also be used for threading pipes and other cylindrical objects.
- Place of Origin:
- Video outgoing-inspection:
- Machinery Test Report:
- Marketing Type:
- Warranty of core components:
- Core Components:
- Key Selling Points:
- Applicable Industries:
- Application:
- Condition:
- Production Capacity:
- Voltage: