news
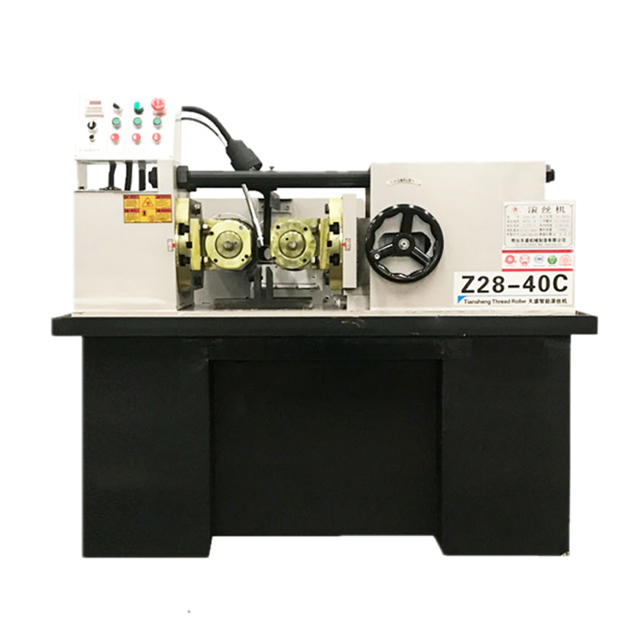
Thread Rolling Machine With Two Shafts
Thread Rolling Machine With Two Shafts
Thread rolling produces accurate threads at high speeds, producing material savings of 15 to 20 percent compared to cutting or turning.thread rolling machine with two shaft The rolling process cold forms the thread from the outside of the workpiece blank, rather than cutting it from the inside. This allows for a larger thread diameter to be formed with less stock, and the displaced metal can actually lengthen the workpiece blank. The rolled thread also has better fatigue resistance than a cut thread, and the finish of a rolled thread is typically much smoother.
The type of machine used for thread rolling depends on the application.thread rolling machine with two shaft When rolling threads on a screw, a cylindrical die head is often the best choice because it can produce a full range of thread sizes and pitches. For more precise applications, a radial thread roll may be necessary. This is especially true when a thread size needs to be accurately centered within the bore of a part or when the end of the part has a shoulder.
A radial thread rolling head can be four times heavier than a cylindrical head and three times more expensive, so only the most precision applications are well-suited to this type of tooling.thread rolling machine with two shaft For example, a radial head is generally used for very fine pitch UNF threads and is not recommended for use on coarse thread sizes. A radial head also requires a very strong drive system to maintain accurate performance over long periods of time, which makes it an inappropriate option for production of a large volume of parts.
During thread rolling, the hardened steel tooth form of the die penetrates the surface of the workpiece blank to reform its profile. These teeth exude extreme pressure against the workpiece, forcing the displaced blank material outward into the thread crests of the dies. This creates a finished thread on the workpiece that is a mirror image of the profile of the die, with the helix angle of the thread incorporated in the die profile.
There are several factors that affect the accuracy of thread rolling, including out-of-tolerance stock dimensions, mismatched rollers and dies, rough roller surfaces, poor feedstock conditioning and incorrect machine settings. In addition, the type of material being rolled can influence its suitability for the process. For example, some materials, such as cast iron, can be difficult to roll, while others, like stainless steel and brass, are good candidates for thread rolling.
When a thread rolling machine is properly configured, 10 to 30 threads per minute can be produced with good accuracy, depending on the thickness of the workpiece blank and the hardness of the material. When the thread to be rolled extends behind a shoulder, a cross-slide knurl-holder should be used; when it extends to a length greater than two-and-one-half times its diameter, a swing roll holder is often preferred. When rolling left hand threads, a left-hand head is required, although standard rolls purchased for right-hand threads can usually be used.
Tags:2d wire bending machine with butt welder | automatic hydrautic thread rolling machine | automatic thread rod machine | automatic thread rolling machine
0users like this.