news
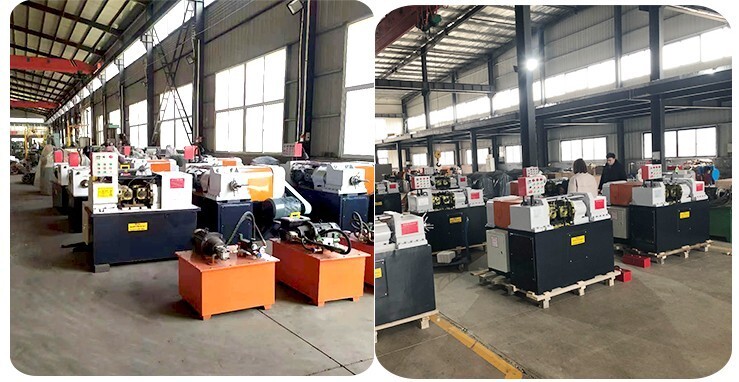
The Newest Thread Rolling Machine For Screw With Free Thread Roller
The Newest Thread Rolling Machine For Screw With Free Thread Roller
Thread rolling produces a thread on a cylindrical part by displacing and raising metal away from the original surface of the stock. This creates helical ridges that give the screw its strength and performance. The ability to roll a thread in one die revolution is important when producing high-speed screws, as is the capacity to produce a consistent quality of thread and die penetration across the length of the workpiece. The ability to accurately adjust or match dies is also essential for the production of a quality thread.
Our newest thread rolling machine for screw with free thread roller is a state-of-the-art system designed to produce up to 3000 nails per minute, thanks to its perfectly engineered feeding and controlling mechanism. It is complemented by an extremely user friendly control panel which allows for simple operation and fast tooling changeovers. It also offers remote connectivity for fast support and supplementary features such as an event logging module and performance tracking module.
All of our threading machines are manufactured to the highest standards and are equipped with the latest software platform from ENKOTEC - ENKOsmart. ENKOsmart enables machine operators to easily and quickly set up the thread rolling process and monitor its performance by means of a touch screen panel. This enables users to view the current setting of the machine and any errors that may have occurred during the production run. In addition, this user-friendly software platform allows for remote connection to ENKOTEC’s customer service team.
In order to guarantee the quality of the finished product, it is vital for the feed system on a thread rolling machine to be perfectly integrated with the rest of the machine. The feeder is used to select and position the blanks before they are transferred into the dies for thread rolling. It is therefore necessary to be able to verify the functionality of the feeding system and ensure that the feeding rails receive a constant flow of correctly positioned blanks.
The base of a thread rolling machine is one of the most critical components because it must be easy to adjust, stable and resistant to vibrations produced by the workpiece. To this end, all INGRAMATIC machines are supplied with a hydrostatic guide system on the slide of the adjusting bolts. This system guarantees a precise and accurate adjustment of the tool holder in order to avoid any deformation of the machine.
All mechanical components of INGRAMATIC machines are machined within the SACMA Group plants, which gives the company full quality control over the parts it manufactures. The use of these advanced machine tools and the careful machining process results in high precision, stability and a long service life. This in turn results in low maintenance costs and increased productivity. For example, the machine bed is made of pearlitic spheroidal cast iron, which guarantees excellent vibration resistance. This also helps to counter the stresses caused by the thread rolling process and reduces thermal stress on the workpieces.
Tags:800kn thread rolling machine | z28-315 thread rolling machine
0users like this.