news
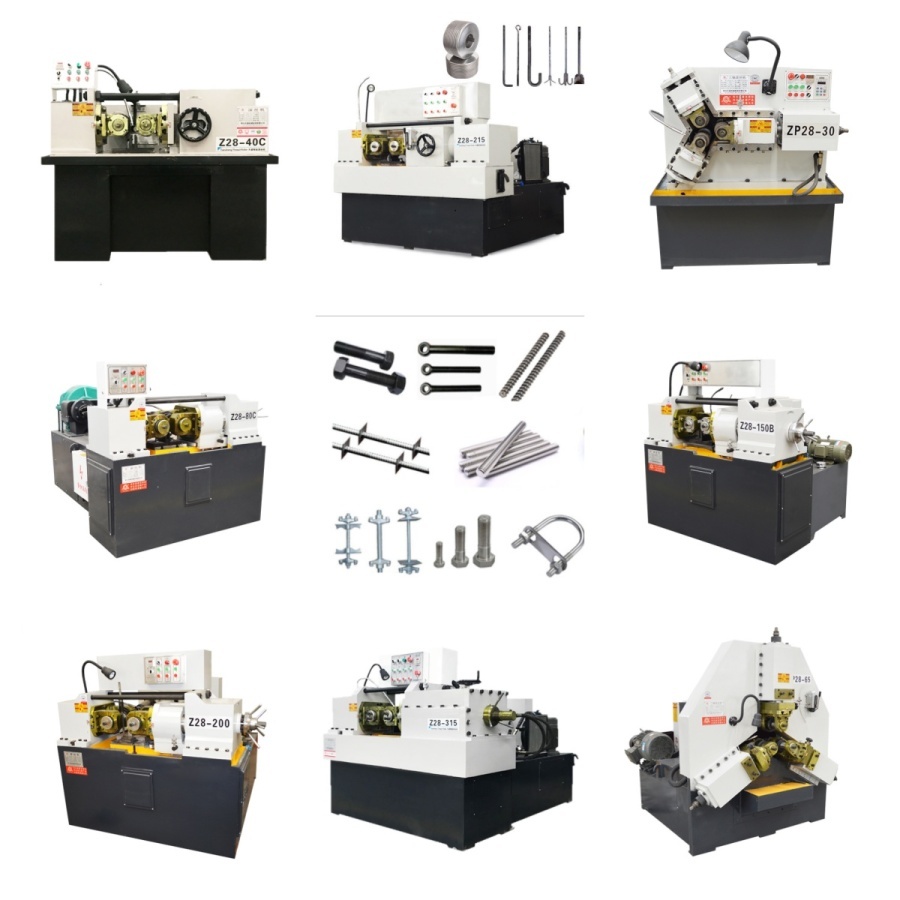
Straight Thread Rolling Machine
Straight Thread Rolling Machine
A straight thread rolling machine is an industrial tool that can form a variety of different threads. Its main purpose is to provide a way for manufacturers to save time and money on the production of parts that need to be threaded. The machine uses a steel roll that is configured to match the desired thread profile, which it then applies to a piece of metal. The resulting threads are stronger, more durable, and more functional than those produced by other methods, including cut threads.
A rolled thread is also harder and more resistant to fatigue, which increases the life of the part and makes it less likely to fail. In addition, the rolling process doesn’t produce waste metal like a cut thread, which can result in cost savings in materials as well as labor costs.
The thread roll used in a straight thread rolling machine is usually made from high-carbon steel. It can be left hand or right hand for American (national) or ISO threads, and it may have a sharp top for rolling an American standard form or a blunt bottom for rolling an ISO form. The diameter of the roll should be slightly smaller than that of the blank or cylindrical part upon which a thread is to be formed. This is to compensate for the extra material that is displaced during the rolling process and raised above the original surface.
In order to roll a thread, the machine must be set up with the proper configuration of dies and workpieces. The threading dies are then placed in a holder that is clamped to the workpiece. The holder should be made from a hard material such as cast iron or steel to ensure that it can withstand the pressure that is applied during thread rolling. The threading dies should be a good fit in the holder, but not so tight that they create an excessive amount of friction.
After the dies are positioned in the holder, the workpiece is then fed into contact with the thread roll at an appropriate feed rate. The feeds to be used are listed in the table “Feeds for Thread Rolling.” The upper half of the table gives the feeds to be used when a cross-slide roll-holder is being used; the lower part of the table gives the feeds when a swing tool is being used.
The helix angles on the dies can vary, depending on whether a tangential or radial thread is being rolled, and on the workpiece material and allowable rate of die penetration per work revolution. In general, 10 to 30 parts per minute are common production rates for a rolled thread. These rates are only possible when the thread rolling dies have been lapped prior to use, to minimize the amount of wear that occurs as a result of the rolling operation. The helix angle on the dies must be close to that of the workpiece thread to produce an accurate, uniform thread.
Tags:steel round bar thread rolling machine | steel bar thread rolling machine | thread rolling machine for steel bar | anchor bolts thread rolling machine with hydraulic system
0users like this.