news
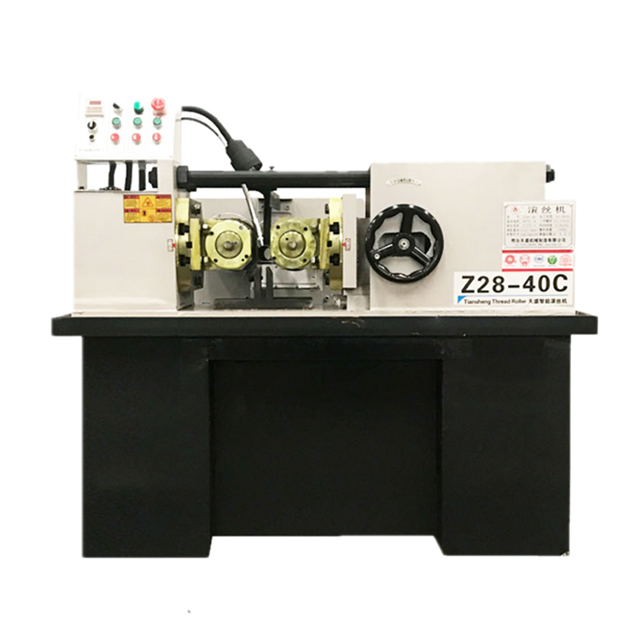
Maintaining a Thread Rolling Machine
Maintaining a Thread Rolling Machine
The thread rolling process produces a thread that is stronger than a cut thread, and it also provides better fatigue resistance.thread rolling machine However, like any machine, it requires regular maintenance in order to function correctly. A few simple tasks, such as lubricating the machine with proper oil and inspecting it regularly for damage, can help ensure that it runs smoothly.
There are two types of thread rolling machines: a flat die type and a plunger feed type.thread rolling machine Both can produce threads in a variety of materials and diameters, although the plunger feed machines are more suitable for rolling hard or difficult-to-roll materials. The basic principle is that the workpiece to be threaded is placed in between a pair of flat or straight dies, with the ridges on the dies inclining at an angle equal to the helix angle of the rolled thread. The dies can be made either milled and ground from solid stock, or grinded from a block after heat treatment.
It is important to select the correct size of blank for a particular job, as the diameter of the finished part is determined by the outside diameter of the screw.thread rolling machine The diameter of the original piece should be larger than the blank, to compensate for the metal that is displaced and raised above the original surface by the thread rolling process. It is common to use rules and formulas to determine the correct blank diameter, but it may be necessary to make minor adjustments in the blank diameter in order to achieve a good-quality rolled thread.
The most important factor in achieving a quality rolled thread is the condition of the stock being used. It must be free of rust, scale, and other impurities. In addition, it should have a low carbon content and a high ductility to allow the material to roll easily. It is also a good idea to cold-work the material before rolling, in order to reduce its hardness and improve its machinability.
Incorrectly sized or conditioned stock can cause a number of defects, including flaking, wavy or uneven crests on the threads, and out-of-tolerance helix angles. Mismatched rollers or dies, incorrect stock feeding, and misalignment between the rollers and the workpiece are other causes of threading defects.
Destructive testing is sometimes required to identify these problems and to verify that the helix angles of rolled threads are within tolerance. A representative sample should be tested at the beginning of each new set up, and periodically throughout production.
In addition to maintaining the appropriate stock and adjusting the rolling speed, it is necessary to maintain a proper cooling system in order to prevent damage to the cylinders and dies. Ideally, the machine should be supplied with a water-soluble emulsified coolant, and ordinary lubricating oil should not be used. This is because the lubricant will react with the steel and form deposits that can lead to thread defects. It is also a good idea to keep the machine clean, and to remove scrap parts from it on a frequent basis.
0users like this.