news
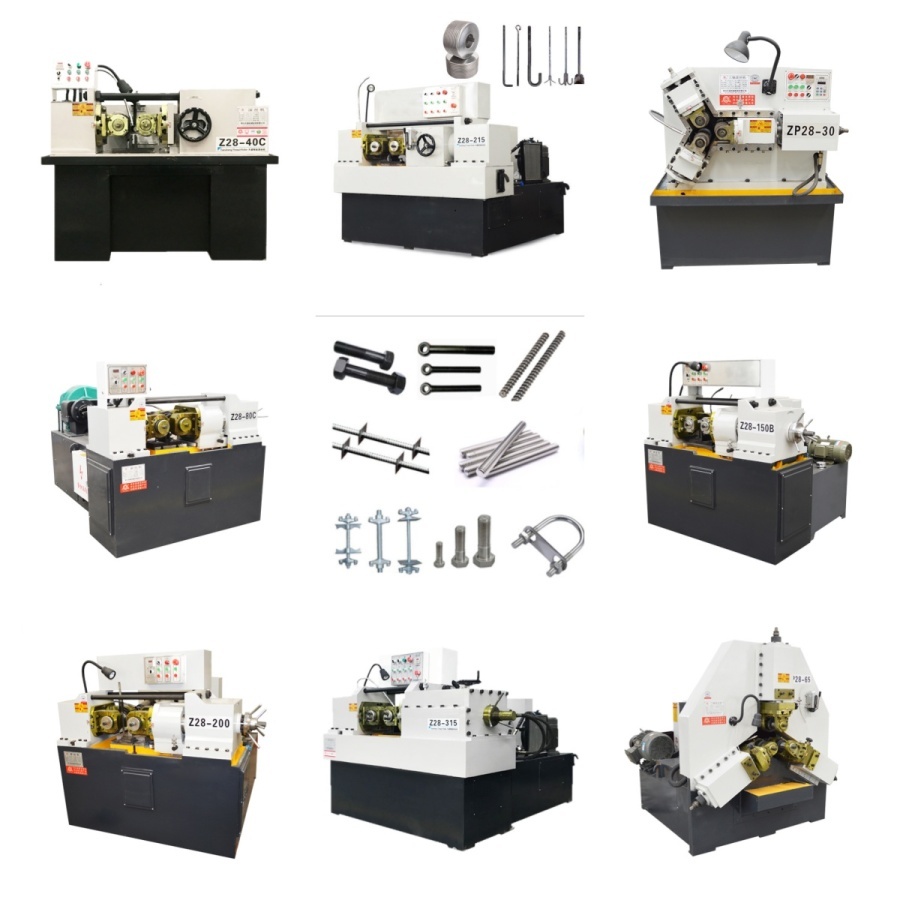
Large Pitch Thread Rolling Machine
Large Pitch Thread Rolling Machine
Thread rolling is a cold-working process that produces superior quality threads than cutting. This is due to the fact that the material is deformed plastically rather than cut, and the resulting threads have better shear strength. The rolling process is also much more economical than the cutting process since it requires no heat to work the metal. However, the quality of a rolled thread depends on the accuracy of the dies used. The selection of the proper head and the appropriate blank size are critical factors in producing the best quality threads. In addition, the design of the part and the relationship that the thread rolling operation bears to other operations is also important.
For best results, it is recommended that the blank diameter of the bar stock be smaller than the rolled thread's major diameter. This is because the thread rolling process displaces a significant amount of material. Blanks that are too large can cause the rolled thread to have an uneven diameter and this will affect the quality of the finished product. Typically, the tolerance for the blank diameter should be equal to one-third of the rolled thread's major diameter.
The forming of the thread itself is another critical factor in the quality of the final thread. Ideally, the corner radii of the rolled thread should be as large as possible in order to promote material flow and minimize stress risers. Also, the pressure and flank angles of the rolled thread should be maintained within certain limits in order to reduce the possibility of cracking.
In order to achieve the optimum thread rolling speeds, the machine must be equipped with a spindle load meter. Using this device, the spindle load can be measured while the feed rate is adjusted. The optimum speed can then be determined by watching the meter and finding the point at which the meter registers the least amount of load. This will be the rpm at which the thread is rolled at maximum efficiency. This method of determining rpm is especially useful in the case of threads that require destructive testing sampling.
A large pitch thread rolling machine is capable of producing threads with a diameter up to 1 1/2 inches (25.4 or 38.1 mm). The production rates of a large pitch thread rolling machine will vary depending upon the hardness of the material, the allowable rate of die penetration per work revolution and the type of blank. Generally, a cylindrical die thread rolling machine is able to produce 10 to 30 parts per minute.
Before starting a thread rolling project, the machine operator must make sure that the machine and the blanks are clean and dry. The blanks must also be sized correctly, which will normally be done by centerless grinding after the thread is rolled. This step is necessary to ensure that the thread rolled will have the desired finish and the correct diameter. The most accurate and best-performing threads are produced on the front of the part, near the end of the bar or blank.
Tags:3 die thread rolling machine | 3 roll thread rolling machine
0users like this.