news
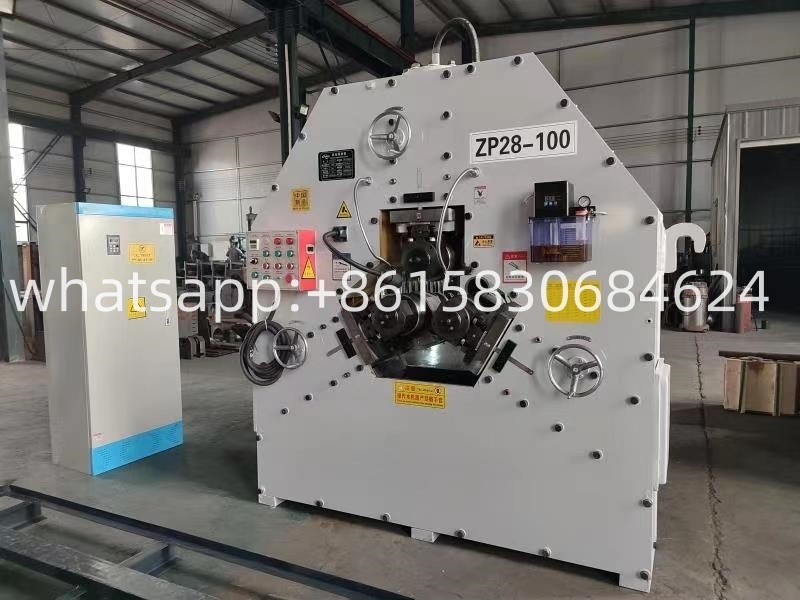
Choosing a Three Axle Thread Rolling Machine
Choosing a Three Axle Thread Rolling Machine
A three axle thread rolling machine is a tool that applies radial pressure to a workpiece while it rotates.three axle thread rolling machine This creates the desired geometrical thread shape and also compresses the parent material. This results in a hardened condition that provides fatigue resistance in the final threaded part. While this is not the same as annealing, it does produce the same result and is an essential step in creating a high-quality finished product. This is especially true when working with very hard materials that are difficult to cut or grind.
While cutting and grinding severs the metal, thread rolling leaves the grain structure of the parent material intact.three axle thread rolling machine Thread rolling also produces a more uniform surface finish than cutting or grinding, and it is often much faster. This can save on labor, raw materials, and overall production costs.
Thread Rolling Speeds
The mechanical and power limitations of a machine as well as the size and type of threads being produced are all important factors when choosing a thread rolling speed. A lower speed can help with the elongation of a thread and can prevent premature damage to dies, workpieces, or the threads themselves. Higher speeds can be used for a greater reduction in cycle time but may cause workpiece deformation and/or excessive stress on the threads.
A good starting blank diameter is critical to the quality of the rolled threads. The starting blank should be about 0.002 inches smaller than the thread's minor diameter. This will give the rolled threads sufficient room to expand to their intended size while still maintaining the proper pitch diameter.
Another factor is the chamfer angle. The chamfer angle of the workpiece should be about 30 degrees from the center line of the thread. This allows the displaced workpiece material to flow above the thread's leading flank and is particularly beneficial for stronger and coarser threads. For softer workpiece materials, a smaller chamfer angle may be necessary in order to maintain thread roll life.
It's essential to use coolants and lubricant on any type of thread rolling equipment. These are needed to remove the heat generated during the forming process, as it can compromise both the dies and the stock material. A lubricant can also reduce friction between the dies and workpiece, which can increase both precision and accuracy and improve the durability of the dies.
The last thing to remember when threading on a three axle machine is to make sure the head is open before starting a job. The best way to do this is by programming a 0.5-second dwell at the end of the z-axis travel. This will allow the front-end assembly to self-feed forward enough to disengage the rollers, thereby opening the head. This is the best method to avoid a jam because it prevents the heads from rubbing against each other and the workpieces. It's also helpful to regularly lubricate the machine following its manufacturer's recommended oil, as it can reduce friction and wear and improve performance.
Tags:800kn thread rolling machine | 650 thread rolling machine | thread rolling machine model z28-40
0users like this.